| | | 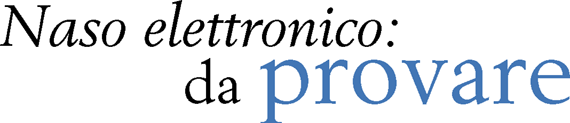 | | Riportiamo i risultati della ricerca condotta al Csi di Bollate (MI), il cui obiettivo è stata la validazione di un sistema di rilevazione delle sostanze odorose emesse da un imballaggio plastico stampato. In alternativa (o dausilio) alle metodologie tradizionali, è stato impiegato un naso elettronico. Gianluigi Vestrucci, Massimo Carugati | |  | | | Tra i principali responsabili dei fenomeni di contaminazione sensoriale, bisogna citare i solventi residui. Al momento attuale, non esistono leggi che descrivano le procedure per la loro determinazione, ma solamente norme volontarie che rimandano, in particolare, alluso di due metodi analitici, ovvero lanalisi strumentale HSGC e lanalisi sensoriale. Entrambe le metodologie presentano alcuni problemi: i tempi di analisi lunghi (soprattutto per i test sensoriali), i costi elevati (in particolare per le analisi HSGC ) e la necessità di impiego di personale specializzato. Lobiettivo del lavoro svolto presso il CSI di Bollate (MI) è stata quindi la definizione - e la successiva validazione - di una procedura per limpiego di un naso elettronico, indicato per la rilevazione delle sostanze odorose rilasciate dagli imballaggi alimentari, in alternativa ai due metodi sopracitati. Parte sperimentale Per raggiungere lobiettivo è stata focalizzata lattenzione sullacetato di etile, il solvente tipico degli inchiostri di stampa rotocalco. La prima ipotesi di procedura era articolata in una fase di calibrazione con acetato di etile puro (figura 1) e in una successiva fase di identificazione (dopo condizionamento) su bobine inquinate dal medesimo solvente. La seconda ha però avuto esito negativo, a causa delle condizioni di termostatazione, che hanno indotto il rilascio di una miscela di sostanze volatili estranea allodore tipico dellacetato di etile puro. Decisamente migliori sono stati i risultati ottenuti con la seconda ipotesi di procedura che prevedeva laddestramento del naso elettronico direttamente con il film plastico inquinato da acetato di etile. Il buon esito della calibrazione (figura 2) e dei successivi test di identificazione effettuati utilizzando questa procedura, hanno indotto i ricercatori a considerarla come la più indicata per lutilizzo del Cyranose 320 in questa applicazione. Procedura finale Lutilizzo del naso elettronico è stato dunque articolato nelle due seguenti fasi: addestramento del naso con bobine contenenti concentrazioni diverse dei solventi inquinanti; identificazione da parte dello strumento sulle bobine inquinate da monitorare. Reali applicazioni della procedura Definita la procedura, essa è stata testata attraverso applicazioni reali e i ricercatori si sono immedesimati nella figura di un ipotetico produttore, che vuole monitorare una propria linea di produzione, e in quella di un utilizzatore, che deve controllare bobine provenienti da produttori diversi. Dalla parte del produttore Per simulare la situazione di un produttore, intenzionato a monitorare una propria linea di produzione, è stata effettuata una calibrazione con bobine della stessa tipologia, ma con concentrazioni diverse di solventi residui. I campioni erano rappresentati da provini tutti della stessa superficie, ma provenienti da bobine con concentrazioni diverse di acetato di etile (tabella 1). Essi sono stati poi suddivisi in base al parametro dellaccettabilità: i gruppi A, B, e C sono stati tutti considerati appartenenti alla classe accettabile, il gruppo D invece rappresentava la classe non accettabile. Questa suddivisione, basata sul contenuto di acetato di etile in mg/m2 nelle bobine, non ha origini di carattere normativo, ma è semplicemente derivata dalla consultazione di capitolati di fornitura nei quali spesso si cita un valore limite di contenuto di solventi residui pari a 10 mg/m2, espresso come acetato di etile. Tutti i campioni sono poi stati condizionati a 100 °C per 40 minuti. La figura 3 mostra lesito della fase di calibrazione. La tabella 2 evidenzia come lo strumento abbia avuto difficoltà solo nella discriminazione tra le classi da 3 mg/m2 e da 6 mg/m2, come hanno dimostrato anche i due errori commessi dal naso nella prova di identificazione proprio in merito a campioni di quelle due classi (tabella 3). Esprimendo però gli stessi dati in un modo più funzionale al tipo di procedura utilizzata, basata sulla creazione di due sole classi distinte tra loro in base al parametro dellaccettabilità, è ancora più evidente come il risultato ottenuto sia stato positivo, avendo ottenuto il 100% delle risposte esatte (tabella 4). I test di confronto Abbiamo a questo punto voluto effettuare anche un test di confronto tra le prestazioni del naso elettronico e quelle del nostro panel aziendale interno di giudici i quali sono selezionati, addestrati al riconoscimento di particolari odori tra i quali anche lacetato di etile e monitorati regolarmente, il tutto secondo norme ISO. Abbiamo pensato che il tipo di test più indicato per effettuare un confronto significativo tra le potenzialità dello strumento e quelle del panel, fosse un test effettuato in base allintensità dellodore di acetato di etile. La prova organolettica è stata dunque allestita preparando i campioni secondo la norma UNI 10192, e cioè introducendo 150 cm2 di bobina in beute da mezzo litro e condizionandole successivamente a 18 °C per 55 ore. Agli assaggiatori è stato richiesto di individuare lesatta sequenza di ordinamento per campioni compresi in un range da 0 a 13 mg/m2. Dai risultati riportati in tabella 5, è possibile osservare come un assaggiatore abbia commesso un errore assimilabile a quello commesso dallo strumento in fase di calibrazione, dovuto alle difficoltà nel discriminare campioni da 3 mg/m2 rispetto a quelli da 6 mg/m2. Un secondo assaggiatore ha invece commesso un errore più grave, in quanto ha scambiato un campione della classe accettabile (da 6 mg/m2) con uno appartenente alla classe non accettabile(13 mg/m2). Dalla parte dellutilizzatore Abbiamo a questo punto cercato di ricreare la situazione di un utilizzatore, che debba controllare bobine provenienti da produttori diversi. A tal fine abbiamo richiesto a tre aziende produttrici di inviarci una loro bobina ritenuta idonea e una bobina della stessa tipologia, ma considerata non conforme a causa di un eccesso di solvente. Lo strumento è stato quindi calibrato con campioni rappresentati da provini tutti della stessa superficie, ma provenienti rispettivamente dalla bobina ritenuta idonea e da quella considerata non conforme di ciascun produttore. Anche in questo caso i campioni sono stati tutti condizionati a 100 °C per 40 minuti. Dalla figura 4 risulta evidente come larea dei campioni accettabili sia chiaramente distinta da quella dei campioni non accettabili. È inoltre visibile, allinterno di queste due grandi classi, anche una parziale discriminazione tra i tre diversi campioni accettabili e tra quelli non accettabili, ma questo fatto più che dalla figura è evidente dalla tabella 6, che ci conferma come nessun campione OK sia stato scambiato per campione NON OK, e che solo pochi campioni non sono stati discriminati correttamente anche a livello delle singole sottoclassi. Il maggior numero di errori in questo senso è stato commesso nella discriminazione di provini contenenti rispettivamente 1 mg/m2 e 1,5 mg/m2. I test di confronto Anche in questo caso è stato allestito un test di identificazione, attraverso il quale volevamo soprattutto verificare la capacità del naso elettronico di distinguere un campione OK da un campione NON OK. In tabella 7 è possibile vedere come il 100% dei campioni siano stati assegnati alla classe corretta. Inoltre l80% dei campioni è stato assegnato correttamente alla specifica sottoclasse (determinata dal diverso produttore) allinterno della grande classe dei campioni conformi o non conformi. Abbiamo ipotizzato che la scarsa affidabilità di alcune risposte fosse da attribuirsi non tanto a difficoltà da parte dello strumento nel riconoscere campioni OK da campioni NON OK, quanto a difficoltà nella discriminazione tra campioni appartenenti alle singole sottoclassi. Per verificare questa ipotesi è stata effettuata una nuova calibrazione (figura 5) con due sole classi: la prima riuniva le bobine idonee dei tre diversi produttori, laltra le tre bobine non conformi. In questo caso il 100% dei campioni sono stati discriminati correttamente (tabella 8) e anche nel successivo test di identificazione (tabella 9) è stato ottenuto il 100% delle risposte corrette, oltre a elevati livelli di affidabilità delle risposte. Anche in questo caso abbiamo voluto fare un confronto tra le prestazioni del naso elettronico e quelle del nostro panel aziendale interno di giudici. Agli assaggiatori è stato richiesto di identificare la sequenza corretta di ordinamento per campioni compresi in un range da 0 a 30 mg/m2. I risultati sono riportati in tabella 10: risulta evidente come un solo assaggiatore sia stato in grado di riconoscere la corretta sequenza, mentre un secondo assaggiatore ha commesso un errore definibile grave in quanto ha scambiato un campione OK ( 3 mg/m2) con un campione NON OK (13 mg/m2). La maggior parte degli errori ha riguardato lordinamento delle bobine considerate non conformi. A parziale giustificazione degli assaggiatori che non hanno saputo riconoscere la corretta graduatoria di intensità bisogna sottolineare che, il numero di campioni da sottoporre ai giudici in un test di ordinamento, non dovrebbe mai essere superiore a cinque; in questo caso abbiamo chiesto di valutarne sei, così da rendere più significativo il confronto con il test effettuato dal naso elettronico (al quale erano stati sottoposti sei campioni diversi senza alcun bianco). È importante inoltre segnalare come alcuni assaggiatori abbiano evidenziato la percezione di sostanze dallodore sgradevole, cattivo e quasi di bruciato che, probabilmente, influenzano la valutazione oggettiva di assaggiatori umani più di quanto non avvenga per il naso elettronico che, a giudicare dai risultati, sembra risentirne di meno. Limiti e vantaggi della procedura I limiti della procedura utilizzata sono da ricondursi essenzialmente a: necessità di disporre di un archivio o magazzino di bobine a diversa concentrazione di solventi residui, per effettuare il training dello strumento; i tempi per portare a termine la procedura ancora piuttosto lunghi (circa 50 minuti complessivamente). È giusto sottolineare però, anche i vantaggi offerti da questa procedura, ovvero: la sua economicità e la conseguente possibilità di un maggiore monitoraggio degli imballaggi; la sua semplicità di applicazione che, insieme alla praticità di utilizzo dello dello strumento, consentono limpiego di personale non specializzato a partire dalla fase di preparazione dei campioni fino ad arrivare allelaborazione dei dati. Possibili sviluppi Alla luce dei risultati ottenuti è possibile concludere che questo naso elettronico - secondo la procedura descritta - non debba essere considerato uno strumento sostitutivo tout court; si tratta in realtà di un valido strumento di supporto ai metodi analitici oggi utilizzati e in particolare allanalisi sensoriale. Gli sviluppi futuri della ricerca potrebbero concentrarsi sulla verifica della possibilità di definire una procedura di utilizzo di questo naso elettronico, che riesca ad esaltarne la caratteristica di portatilità, favorendone limpiego al di fuori di un laboratorio a vantaggio di analisi effettuate direttamente sul campo. Gianluigi Vestrucci (Responsabile Divisione Chimica-Fisica e Microbiologia CSI) Massimo Carugati CSI S.p.A. (Gruppo IMQ) Bollate (MI) |  | Electronic nose: testing We here relate the results of the research carried out at Csi of Bollate (MI), whose objective was the validation of a system for recording the odorous substances emitted by printed plastic packaging. Alternatively (or additionally) to the traditional methodologies, an electronic nose was used. Residual solvents are among the chief causes of the phenomena of sensory contamination. At this moment in time there are no laws regulating procedures for their determination but only voluntarily respected rules which refer, in particular, to the use of two analytical methods, or rather the HSGC instrumental analysis and the sensory analysis. Both methodologies present some problems: the lengthy analysis times (primarily for sensory tests), the elevated costs (in particular for the HSGC analyses) and the need to use specialised personnel. The objective of the work carried out at the CSI of Bollate (MI) was therefore the definition and the subsequent validation- of a procedure for the utilisation of an electronic nose, indicated for the recording of odorous substances released by food packaging, as an alternative to the two methods mentioned above. Experimental phase In order to reach the objective attention was focussed on ethylene acetate, the typical ink solvent used in rotogravure print. The initial procedural hypothesis was divided into a calibration phase using pure ethylene acetate (figure 1) and a subsequent identification phase (after cooling) on spools polluted in the same solvent. The second phase produced a negative result however due to the thermostatic conditions which induced the release of a mixture of volatile substances unlike the typical odour of pure ethylene acetate. Decidedly better results were obtained by the second procedural hypothesis which envisaged training the electronic nose using the plastic film polluted in ethylene acetate directly. The good results produced by the calibration phase (figure 2) and the subsequent identification tests carried out using this procedure, led the researchers to conclude it was the most suitable for the utilisation of the Cyranose 320 in this application. Final procedure The use of the electronic nose was therefore divided into the two following phases: training the nose using spools containing different concentrations of the polluting solvents; identification of the polluted spools to be monitored by the same instrument. Real applications of the procedure Once the procedure was defined it was tested on possible real applications and, in order to do this, the researchers put themselves in the place of a hypothetical producer who wants to monitor his production lines and a user who must check spools coming from different producers. On the side of the producer To simulate the situation of a producer intending to monitor his production line a calibration with spools of the same typology but having different concentrations of residual solvents was carried out. The samples were represented by specimens all of the same surface area but coming from spools having different concentrations of ethylene acetate (table 1). These were then subdivided on the basis of the parameter of acceptability: groups A, B and C were all considered to belong to the acceptable category, group D on the other hand represented the unacceptable category. This subdivision, based on the content of ethylene acetate in mg/m2 in the spools does not have a legal nature but simply derives from the consultation of supply specifications in which there is often an upper value of residual solvent content equal to 10 mg/m2 expressed as ethylene acetate. All samples were then cooled to 100°C for 40 minutes. Figure 3 shows the results of the calibration phase. Table 2 shows how the instrument had difficulty only in discriminating between the categories 3 mg/m2 and 6 mg/m2 as the two errors made by the nose in the identification test of sample in those two categories showed (table 3). Expressing however the same data in a more practical way considering the type of procedure used, based on the creation of just two categories distinct from each other on the basis of the parameter of acceptability, it is even more evident how positive the result obtained was, having achieved 100% exact responses (table 4). Comparison tests At this stage we wished to carry out a test comparing the performance of the electronic nose and the performance of our internal company panel of judges who are selected and trained to recognise particular odours including ethylene acetate and regularly monitored, according to ISO regulations. We thought that the most suitable type of test for making a significant comparison between the potentiality of the instrument and that of the panel was to do a test based on the intensity of the ethylene acetate odour. The organoleptic test was therefore set up by preparing the samples in accordance with the UNI 10192 regulation, and that is putting 150 cm2 of spool in Erlenmeyer flasks of half a litre and subsequently cooling them to 18°C for 55 hours. Samplers were asked to identify the exact sequence of ordering for samples included in a range from 0 to 13 mg/m2. From the results shown in table 5 it can be observed how a sampler made a similar error to the error made by the instrument in the calibration phase, owing to the difficulty of discriminating between samples of 3 mg/m2 and 6 mg/m2. A second sampler instead made a more serious error confusing a sample belonging to the acceptable category with one belonging to the unacceptable category (13 mg/m2). On the side of the user At this point we tried to recreate the situation of a user who must check spools coming from different producers. To this end we asked three manufacturing firms to send us one of their spools considered fit and a spool of the same typology considered unfit due to a surplus of solvent. The instrument was therefore calibrated with samples consisting of specimens all having the same surface area but taken respectively from the spool considered fit and the one considered unfit by each producer. In this case too all samples were cooled to 100°C for 40 minutes. From figure 4 it is obvious that the area of acceptable samples is clearly distinct from the unacceptable one. Moreover within these two large categories a partial discrimination between the three different acceptable samples and the three unacceptable ones can be seen, but this fact is more evident from table 6 than from the figure which confirms that no OK sample was taken for a NOT OK sample and that only a few samples were not chosen correctly even in the subcategories. Here the majority of errors were made in choosing the specimens containing respectively 1 mg/m2 and 1.5 mg/m2. Comparison tests In this case too an identification test was set up, with which we wished primarily to verify the ability of the electronic nose to distinguish an OK sample from a NOT OK sample. In table 7 one can see that 100% of the samples were assigned to the correct category. Moreover 80% of the samples were assigned correctly to the specific subcategory (determined by the different producer) within the larger category of fit or unfit samples. We postulated that the poor reliability of some responses was attributable not so much to the difficulty of the instrument in distinguishing OK samples to NOT OK samples but to the difficulty of discriminating between samples belonging to the individual subcategories. To verify this hypothesis a further calibration was carried out (figure 5) on just two categories: the first grouped the fit spools of the three different producers, the other the three unfit spools. Here 100% of the samples were chosen correctly (table 8) and in the subsequent identification test too (table 9)100% correct answers were obtained, in addition to the elevated level of reliability of the answers. Here too we wished to compare the performance of the electronic nose with that of our internal panel of company judges. The samplers were asked to identify the correct sequence of ordering for samples included in a range from 0 to 30 mg/m2. The results are related in table 10, where we see that just one sampler was able to identify the correct sequence while a second sampler made a error which might be defined serious confusing an OK (3 mg/m2) sample with a NOT OK sample (13 mg/m2). The majority of errors concerned the ordering of the spools considered unfit. To partially justify the samplers who were unable to recognise the correct measure of intensity it must be emphasised that the number of samples submitted to the judges in a test of ordering should never exceed five; in this case we asked them to evaluate six so as to make the comparison with the test carried out by the electronic nose (to which six different samples without any blanks were submitted) more significant. It is moreover important to note how during their evaluation some samplers emphasised their perception of substances having an unpleasant, bad and almost burnt odour which probably influence the human samplers objective evaluation more than the electronic noses which, to judge by the results, appears to be less affected. Limits and advantages to the procedure The limits of the procedure used can essentially be linked to: the need for an archive or store of spools with different concentrations of residual solvents in order to train the instrument; the rather lengthy times required for carrying out the whole procedure (about 50 minutes altogether). However it is also correct to underline the advantages offered by this procedure, which are: its low cost and the consequent opportunity to increasingly monitor of the packaging; the simplicity of its application which, along with its practicality of use, allows the use of non specialised personnel from sample preparation to data elaboration. Possible developments In the light of the results obtained it may be concluded that this electronic nose according to the procedure described- should not be considered an substitutive instrument tout court; in reality it is a valid support instrument for the analytical methods used today and in particular sensory analysis. Future research developments could concentrate on exploring the possibility of defining a procedure of use for this electronic nose which might increase its portability, favouring its use outside the laboratory to the benefit of analyses carried out on site. Gianluigi Vestrucci (Chief of the Chemical-Physics and Microbiology Division), Massimo Carugati CSI S.p.A. (IMQ Group) Bollate (MI) | | |  | Cyranose, uno strumento da addestrare Il naso elettronico utilizzato durante la sperimentazione è stato il Cyranose 320 (nella foto). La principale componente dellhardware di questo strumento è la matrice costituita da 32 sensori polimerici drogati con carbon-black (un materiale conducente). Quando viene esposto ai vapori, ciascun sensore si dilata provocando una variazione di conducibilità al proprio interno. La resistenza passa quindi da R0, rilevata sul resistore al momento del passaggio dellaria per la linea di base, a RMAX, che è diversa per ogni sensore e viene determinata al momento del passaggio della soluzione gassosa da testare. Il software a questo punto, in base al segnale elettrico prodotto da ciascun sensore, calcola per ognuno di essi il rapporto (RMAX - R0)/R0 e unisce le 32 risposte, producendo così la smellprint (impronta olfattiva) del campione analizzato. Successivamente, questa impronta verrà confrontata dallo strumento con quelle di altri campioni. La modalità di utilizzo del naso elettronico non può prescindere da: una fase di addestramento (per creare un database di impronte olfattive digitalizzate); una fase di identificazione dei campioni incogniti (tramite confronto delle loro impronte olfattive con quelle conservate in memoria). |  | Cyranose, an instrument to be trained The electronic nose used during the experimental phase was the Cyranose 320 (in the photo). The principal component of this instruments hardware is the matrix made of 32 polymeric sensors doped with carbon-black (a conducting material). When it is exposed to vapours, each sensor dilates provoking an internal variation of conductivity. The resistance therefore passes from R0, detected on the resistor at the moment of the passage of air on the basic model , to RMAX, which is different for each sensor and is determined at the moment of the passage of the gaseous solution to be tested. At this point the software, on the basis of the electric signal produced by each sensor, calculates for each of these the ratio (RMAX - R0)/R0 and unites the 32 responses, producing thus the smellprint of the analysed sample. Subsequently this print will be compared by the instrument with those of other samples. The modality of use of the electronic nose must include: a training phase (to create a database of digitised smellprints); an identification phase of the unknown samples (through a comparison of their smellprints with those stored in the memory). |  | |  | | |