| 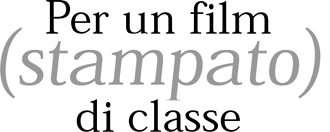 | | Nuovo stabilimento, nuovi uffici, nuova macchina da stampa flexo a 8 colori. Così ITP celebra 29 anni di attività e i successi nel campo dellestrusione e stampa di film termoretraibile, skin e per accoppiamento. Suggestioni dallincontro-dibattito che ha riunito amici e fornitori per festeggiare insieme, con costrutto. Stefano Lavorini | | | 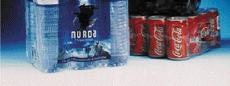 | | | Siamo ormai assuefatti alla schizofrenia della quotidianità, alla vorticosa velocità dei cambiamenti di stile di vita imposti dalla tecnologia, alla pervasiva logica del mercato e del profitto: Tutto, ora e subito, sembrerebbe essere la parola dordine di questi tempi moderni, prendendola a prestito, senza alcuna considerazione, da un vecchio slogan della contestazione studentesca. Eppure resistono e prosperano realtà di successo che hanno il coraggio di seguire percorsi autonomi, forse strade più impervie, e che sanno coniugare la consapevolezza del presente con sentimenti come correttezza, spirito critico, trasparenza, senso del dovere nei confronti propri e degli altri. Ce ne siamo accorti in occasione dellincontro organizzato a giugno da ITP-Industria Termoplastica Pavese SpA per dibattere, in un confronto informale tra fornitori e clienti, delle nuove tecnologie relative alla stampa flessografica. Un modo intelligente per festeggiare con numerosi invitati, tra cui ospiti stranieri e bei nomi dellimprenditoria lombarda, linaugurazione della nuova area produttiva e della nuova macchina da stampa flessografica a otto colori. Dallestrusione alla stampa Fantasia, bellissima sirena, macchina eccezionale che ci porta dove non si può andare
così canta il cantastorie e così forse ha creduto Nicola Centonze quando, nel 1972, fondò la ITP: una piccola realtà di poco più di dieci persone, con una casa colonica per ufficio, che oggi è diventata unazienda da 140 addetti, con una capacità produttiva in estrusione di circa 25.000 t/anno, una potenzialità di stampa - con linserimento della nuova macchina - di 6000 t/anno, e un fatturato di 80 miliardi (previsioni per il 2001). Al di là delle cifre, certo è che Centonze, ripercorrendo con emozione le tappe di questo cammino, si è preoccupato più di ricordare laiuto ricevuto agli inizi da alcuni fornitori, che di celebrare i propri successi. «Quando siamo nati lapprovvigionamento di materie prime è stato un problema, perché pochi erano disposti a fornire materiale a una piccola realtà come la nostra. Ma siamo stati fortunati e abbiamo trovato aziende che hanno creduto nelle nostre capacità, come la Basf (oggi Basel) che per molti anni è stata il nostro fornitore unico e tuttora resta il principale. Analogamente, sul piano commerciale siamo in relazione da 25 anni con la francese Soretrac - oggi uno dei primi distributori europei di materiale per limballaggio - con cui abbiamo iniziato la penetrazione sui mercati esteri. In questo modo siamo cresciuti fino ad avviare, nel 1980, la produzione di materiali stampati, che andavano in quel momento affermandosi sul mercato. In verità, allinizio avevamo pensato che la stampa sul termoretraibile fosse una moda passeggera, ma ci siamo dovuti ricredere. Così abbiamo preso un primo impianto per la stampa a 6 colori, a cui successivamente abbiamo aggiunto altre unità per decidere infine, lanno scorso, di acquistare la nuova macchina e di costruire ex novo un capannone dove collocarla». Per una produzione di qualità Oggi il sito ITP è strutturato in due parti, in cui trovano posto le linee di estrusione e le macchine da stampa, ma sono già stati acquistati alcuni terreni adiacenti, in previsione di ulteriori sviluppi. Massimo Centonze, responsabile Qualità, così spiega: «La produzione si articola in 4 fasi: estrusione, stampa, ribobinatura e rigenerazione. La prima si sviluppa in due zone successive, rispettivamente dedicate alla realizzazione di film termoretraibile e skin, con 6 linee di estrusione a 1 e 3 strati, e ai film per alimenti, con coestrusori a 3 e 5 strati. Per quanto riguarda la stampa, disponiamo invece di due linee flexo, accanto a cui lavorano 4 ribobinatrici, di cui una con sistema di stampa a 2 colori, e 1 taglierina. Infine, limpianto di rigenerazione è costituito da un estrusore accanto a cui opera limpianto per il riciclo di materiali particolari». «In questo contesto - quantifica Umberto Valente, direttore commerciale della ditta - il termoretraibile rappresenta circa 10.000 t e impegna una buona parte della capacità produttiva attuale, insieme ai film per accoppiamento, barriera, pelabili e antifog (più o meno altre 10.000 t) e ai film per skin packaging industriale. Il nuovo impianto W&H verrà utilizzato per stampare polietilene e soddisfare le crescenti richieste di materiali per promozioni e personalizzazione, vista la saturazione della macchina precedente (circa 3.000 t)». Ma gli investimenti non si limitano allimpiantistica: come precisa Massimo Centonze, ITP ha implementato una serie completa di controlli - dalla materia prima, al processo e al prodotto - e di procedure che hanno portato alla certificazione ISO 9002 e (entro la fine dellanno) ISO 14000 sullambiente. Per non parlare delle maestranze, considerate sin dagli inizi la risorsa primaria dellazienda: «nel 1999 sono state dedicate alla formazione 1.500 ore e lanno successivo circa 2.200, anche grazie al ciclo continuo su 5 turni che lascia spazio alle attività di aggiornamento professionale». | | A top class (printed) film New works, new offices, a new 8 color flexo print machine. This is how ITP is celebrating its 29 years of activity and its successes in the field of the extrusion and printing of heatshrink film, skin film and film for bonding. Constructive suggestions from the get-together cum debate attended by friends and suppliers. We are by now addicted to the schizophrenia of the everyday, of the heady speed of changes to our lifestyle imposed by technology, to the all-pervasive logic of the market dictated by profit: Everything, now and straight away would seem to be the watchword of these modern times, borrowing without consideration an old slogan from the times of student unrest. Though all the same successful concerns that are brave enough to follow their own way resist and prosper. These may perhaps take the steep and stony path, while all the same reconciling awareness of the present with sentiments such as straightforwardness, a critical spirit, transparency, a sense of duty to oneself and to others. We noticed the same in the occasion of the meeting organised in June by ITP-Industria Termoplastica Pavese SpA, an informal get-together between suppliers and customers offering a chance to exchange opinions on the new flexographic print technology. Indeed an intelligent way to celebrate the inauguration of the new area for production and the new eight color flexographic print machine; attendance was numerous, including many foreign guests along with big names of Lombard entrepreneurism. From extrusion to print Imagination, oh beauteous siren, extraordinary machine that brings us where we cannot go... go the words of the balladeer, and this is probably what Nicola Centonze believed when, in 1972, he set up ITP: a small concern of a little over ten persons with a country house for an office that today has become a company with 140 employees, with an extrusion production capacity of around 25,000 t/year, a print potential - with the insertion of the new machines - of 6000 t/year, and a turnover of 80 billion (forecasts for 2001). Over and beyond the figures, certainly Centonze, reminiscing on the various stages, showed himself more intent on remembering the help received at the outset from given suppliers than in celebrating his own successes. «When we came into being, the procurement of raw materials was a problem, because few people were prepared to supply a concern as small as ours was. But we were lucky to find firms that believed in our capabilities, such as Basf (today Basel), our sole supplier for many years and still our main supplier to date. In the same vein, on the commercial side of things we have had exchanges with the French company Soretrac for the last 25 years - today one of the main European distributors of packaging material - with which we started up our penetration of foreign markets. Thus we managed to grow, up to starting up the production of printed material in 1980, that at that time was enjoying success on the market. Truth to say, at the outset we thought that print on heatshrink was but a passing fashion, but we were forced to change our minds on that. Thus we took on our first 6 color printer, to which after that we added other units; in the end last year we decided to buy the new machine and rebuild the shed to house it from scratch». Towards a quality production Today ITPs worksite is structured in two parts, hosting the extrusion lines and print machines, yet the adjacent grounds have already been bought up in view of further development. Quality head Massimo Centonze explains: «Production is done in 4 phases: extrusion, print, rewinding and regeneration. The first is developed in two successive zones, respectively dedicated to the creation of heatshrink and skin film, with 6 single extrusion lines and 1 or 3 layer lines, and film for foodstuffs, with 3 and 5 layer coextruders. As far as the print is concerned, we have two flexo lines accompanied by 4 rewinders, one of which with a 2 color print systems and one cutter. Finally, the regeneration plant is made up of an extruder accompanied by a system for recycling special materials». As Umberto Valente, commercial head of the company, states «heatshrink accounts for around 10,000 t and commits a large part of our current production capacity, along with films for bonding, barrier, pealable and antifog films (more or less another 10,000 t) and film for industrial skin packaging. The new W&H system will be used for printing polyethylene and to satisfy the growing demand for materials for promotion and personalization, given the saturation of the preceding machine (around 3,000 t)». But investments are not limited to facilities: as Massimo Centonze goes on to say, ITP has implemented a whole series of controls - on raw material as well as on the process and product - and to procedures that have led to ISO 9002 certification and (by the end of the year) ISO 14000 environmental certification. Not to speak of the workforce, considered the companys primary resource right from the outset: «in 1999 some 1,500 hours were dedicated to training and 2,200 the year after that, thanks also to the companys continuous 5 shift cycle that leaves space for professional updates». | | | Flexo über alles ITP ha voluto dedicare lincontro svoltosi in giugno presso il proprio stabilimento di Bosnasco (PV) alla stampa flessografica, alla sua evoluzione in questi ultimi anni e ai suoi sviluppi nel breve periodo. Fra i relatori, nomi autorevoli: Bosse e Wallmann, responsabili estrusione e stampa in Windmöller & Hölscher, ed Enrico Vogogna, amministratore delegato della filiale italiana; Ripamonti (Nuova Roveco), Albani (DuPont), Pasquarelli (Unionplast) e, per lazienda ospite, il presidente delegato Nicola Centonze, il responsabile qualità Massimo Centonze e il direttore commerciale Umberto Valente. Si è parlato della necessità di utilizzare impianti di estrusione altamente automatizzati, in grado di ridurre i margini di errore umano e di produrre supporti con superiori caratteristiche ottiche, di distribuzione dello spessore, di planarità e di tollerenza nei valori di retrazione. Quindi è stata esaminata la nuova macchina flessografica Astraflex DD, esaltando i plus di capacità produttiva, qualità di stampa e flessibilità. A titolo dimostrativo, sono stati riprodotti in maniera impeccabile 2 soggetti Coca Cola - a 7 e 8 colori lavorando a 300 m/min, con ampi fondi pieni e su una luce di 1.050 mm (1.090 di sviluppo). Ma si è anche discusso, più in generale, di evoluzione della tecnologia digitale, fotopolimeri e lastre e prove di stampa digitali, di sleeve, di qualità argomentando, in definitiva, della sempre maggiore competitività della flexo rispetto alla roto e della necessità di riconsiderare luoghi comuni spesso duri a morire. | | Flexo über alles ITP dedicated the get-together held in June at its works at Bosnasco (PV) to flexographic printing, to its evolution over the last few years and to its short-term development. The speakers included some names of note: Bosse and Wallmann, extrusion and print head at Windmöller & Hölscher, and Enrico Vogogna, managing director of their Italian branch; Ripamonti (Nuova Roveco), Albani (DuPont), Pasquarelli (Unionplast). President Nicola Centonze, Quality head Massimo Centonze and commercial director Umberto Valente representing the host company. One spoke of the need to use highly automated extrusion systems, capable of reducing the margins of human error and to producing supports with top grade optical qualities, evenly spread out in terms of thickness, even and within shrink tolerances. Hence they went on to examine the new Axtraflex DD flexo machine, exalting its production capacity, print quality and flexibility. As a demonstration of the same, 2 Coca Cola subjects were reproduced to a T to 7 and 8 colors - working at 300 m/min, on heavy solid and over a width of 1050 (1090 development). But in more general terms one also discussed the evolution of digital technology, photopolymer and digital print test plates as well as sleeves and quality, definitively reflecting on the every greater competitivity of flexo compared to rotogravure, and the need to reconsider clichés that are often hard to overcome. | | |  | Astraflex DD La nuova macchina da stampa flessografica della Windmöller & Hölscher, con tecnica di motorizzazione diretta per il settore a fascia larga, rappresenta probabilmente la summa dellevoluzione tecnologica in questo campo. Si tratta di ununità modulare con 6, 8 o 10 gruppi colore, dotata di robot per il cambio automatico del lavoro. In ITP è stata installata una 8 colori, con larghezza di stampa di 1570 mm, e sviluppi da 400 a 1200 mm, in grado di raggiungere una velocità di stampa e non di macchina di 460 m/min, con una precisione di registro di +/- 0,04 mm. Tra i principali vantaggi della motorizzazione diretta figura il fatto che i cilindri sono azionati da motori singoli e non sono dunque più vincolati con ingranaggi al tamburo centrale. In particolare, questo permette di regolare il passo di stampa in modo infinitesimale, senza alcuna limitazione, con una ridotta manutenzione e risparmio nei tempi di allestimento. Inoltre, il cambio bobina può essere effettuato automaticamente in piena velocità. La macchina è dotata di sistema di regolazione automatico dei gruppi colore, con motore passo passo e aste filettate ad altissima precisione, che permette lavvicinamento dei gruppi stampa con tolleranze micrometriche. La progettazione molto compatta del gruppo elimina le vibrazioni anche ad alta velocità. Lasciugatura dellinchiostro è assicurata da un sistema Enpro con ricircolo dellaria a 2 circuiti e controllo LEL, raggiungendo bassissimi livelli di residuo solvente nella stampa. Secondo i costruttori la Astraflex DD è in grado, grazie al sistema automatico di cambio formato Ecoplus, di passare in circa 20 minuti da un lavoro a 6 colori a un altro analogo, assicurando nel complesso maggiore produttività, tempi di allestimento minori, migliore qualità e flessibilità. E che sia adottata in ITP suona come una conferma. | | Astraflex DD The new Windmöller & Hölscher flexographic print machine with direct motorization for sectors requiring wide web, is probably the top in terms of technological evolution in this field. We are speaking of a modular unit with 6, 8 or 10 color units, fitted with robot for automatic work change. An 8 color has been installed in ITP, with a print width of 1570 mm and development of 400 to 1200 mm, capable of reaching a print speed - not a machine speed - of 460 m/min, with a register accuracy of +/- 0.04 mm. Among the main advantages of the direct motorization one has the fact that the cylinders are directed by single motors and are not hampered by the gearwheels of the central drum. In particular, these enable the detailed regulation of the print step, without limitation, with reduced maintenance and reduction of set up times. As well as that the reel change can be carried out automatically while the machine is running at full speed. The machine has an automatic regulation of the color unit, with step motor and high precision threaded bars, that enable the print unit to be drawn into position micrometrically. The highly compact design of the unit eliminates vibrations even at high speeds. Ink drying is ensured by an Enpro system with dual circuit air recirculation and LEL control, attaining extremely low levels of solvent residue in printing operations. According to the builder, thanks to its automatic system of Ecoplus format change, the Astraflex DD is capable of going from a 6 color job on to a similar job in around 20 minutes, ensuring overall greater productivity, shortened set-up times, better quality and flexibility. And the fact that the machine has been taken on by ITP is something of a confirmation of these features. | | | |