|
|
|
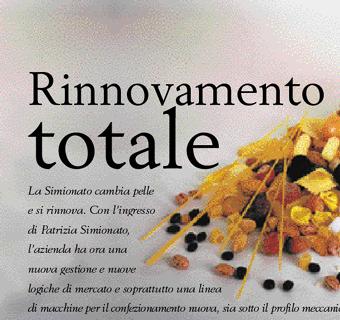 |
Spesso la vita mette a dura prova capacità e forze e può capitare che, riflettendo su quanto si è fatto, si rimanga sorpresi.
Ne è un esempio la storia di Patrizia Simionato che, nellottobre del 2000, prende unimportante decisione e accetta di assumere la presidenza della Simionato S.p.A., cambiando profondamente la sua vita. Non è un semplice passaggio generazionale, lingresso avviene infatti a seguito dellimprovvisa e dolorosa scomparsa del padre Paolo, fondatore della società, e significa abbandonare lattività, svolta da anni, come consulente per limplementazione di sistemi ISO 9000 e docente sul tema qualità.
Il valore degli affetti, la forza di volontà e la determinazione la portano quindi ad accettare la sfida e ad occuparsi a tempo pieno dellazienda, provandosi in un compito che non aveva mai svolto prima, mettendo in gioco se stessa e andando contro tutto e tutti.
I risultati sono andati ben oltre le più rosee aspettative, portando la società di Mestrino (Padova) - specializzata nella costruzione di confezionatrici verticali e inclinate, pesatrici lineari e a combinazione, dosatrici, contapezzi, controlli peso e sistemi di caricamento e trasporto prodotto - a trovare nuovo impulso e vigore.
«Entrando in azienda - ci confessa Patrizia Simionato - ho voluto dare continuità al lavoro di mio padre, ma sono stati determinanti anche il sentimento e la partecipazione dimostratemi dai dipendenti. Ho pensato inoltre a tutte le altre realtà che da tempo gravitavano a vario titolo attorno alla Simionato e ho deciso di trasformare levento così triste in un momento di cambiamento e di crescita, sia per la società, sia per le persone che vi lavoravano».
Di cambiamenti in effetti ce ne sono stati e non hanno toccato solo la struttura amministrativa e commerciale, ma anche la creazione di un ufficio interno per la progettazione elettronica e meccanica. Il risultato è stato in primis la messa a punto di una nuova elettronica per tutte le macchine fino ad arrivare alla revisione del layout di produzione e, nel giro di qualche mese, alla costruzione di una nuova linea di confezionamento, che risponde appieno alle attuali esigenze di flessibilità e affidabilità espresse dal mercato.
Nuova elettronica, nuova meccanica
«Mio padre - ci racconta Patrizia - sebbene non fosse un tecnico e non disponesse in azienda di una struttura dedicata alla progettazione (disegnava in scala e costruiva i relativi modelli col Meccano), era sempre riuscito, grazie alle sue capacità di inventiva e di intuizione, a creare dei prodotti competitivi in grado di collocarsi in una fascia medio-alta di mercato».
Questo fatto non ha però agevolato la figlia quando si è trovata a gestire il delicato passaggio generazionale: il ricorso a strutture esterne sia per la progettazione meccanica, sia per la realizzazione delle schede elettroniche da montare sulle macchine, infatti, non aveva creato i presupposti per la maturazione di competenze specifiche in azienda.
«I primi mesi del 2001 sono stati quelli più faticosi - ci confessa limprenditrice - sia per le difficoltà incontrate nel reperire alcuni componenti che servivano ad assemblare le schede destinate alla costruzione dei macchinari, sia perché in questi casi il mercato sta a guardare levolversi degli eventi.
Fortunatamente, nel 1998, mio padre aveva costituito una struttura interna di ricerca e sviluppo per la progettazione della parte elettronica delle macchine. I risultati di questo impegno si sono concretizzati proprio nel 2000, con una nuova elettronica che ci ha permesso di ridurre notevolmente il numero dei componenti, ma soprattutto di utilizzare uninterfaccia utente uguale per tutte le macchine e, in più, testata per funzionare in condizioni estreme di utilizzo (con temperature di esercizio tra -10 e +70 °C).
Siamo comunque in grado, nel caso ci venga richiesto dallutilizzatore, di integrare un interfaccia utente di commercio».
Compiuto questo primo passo è stata necessaria una buona dose di coraggio per rischiare ancora una volta tutto.
«I tempi erano strettissimi - ricorda Patrizia Simionato - e ho dovuto riorganizzare lazienda e contemporaneamente le macchine, pensando un prodotto nuovo per riconquistare quote di mercato. E abbiamo deciso di farlo creando una struttura interna che, lavorando inizialmente in collaborazione con realtà esterne specializzate, ci ha permesso, successivamente, di integrare in azienda le professionalità necessarie».
Razionalizzare i flussi
Per ridurre il time to market e rendere più competitiva lazienda è stato rivisto anche il layout di produzione, e questo ha comportando anche una diversa assegnazione dei compiti e delle responsabilità.
«Abbiamo pensato - puntualizza Patrizia Simionato - che fosse più efficace e vantaggioso lavorare su commessa, producendo preassemblati per lotti. In questo modo, le persone non vengono impegnate in modo ripetitivo nella produzione delle stesse attrezzature o del singolo componente, ma lavorano sullimpianto nel suo complesso, migliorando così le proprie capacità. Il vantaggio principale è che, curando lallestimento dellimpianto ed eseguendo anche il collaudo delle macchine, tutti gli addetti in produzione, se necessario, ora sono in grado di effettuare anche lassistenza tecnica. Ma non solo.
Cambiando metodologia di lavoro, possiamo realizzare unestrema personalizzare delle linee, elemento di non poco conto, dato che la Simionato opera ad ampio raggio nel settore alimentare, dove le esigenze variano moltissimo a seconda del comparto (da quello della pasta e del dolciario a quello dei surgelati, dalle carni alle verdure, passando per i prodotti in polvere e granulari)».
Modificando il layout di produzione si è poi resa necessaria ladozione di un magazzino dinamico in grado di rispondere alle nuove esigenze.
«Abbiamo cercato di razionalizzare tutti i flussi gestendo, da una parte, lingresso delle materie prime e, dalla parte opposta, la spedizione delle macchine finite; abbiamo anche adottato un nuovo sistema di gestione che consente di identificare, tramite codice a barre, ogni pezzo a magazzino».
La forza del personale
Di pari passo con la revisione dellattività produttiva, Patrizia Simionato si è trovata impegnata anche sul fronte, non meno impegnativo, della riorganizzazione del personale. A questo proposito ha giocato un ruolo fondamentale la capacità dellimprenditrice di saper guardare oltre, responsabilizzando e motivando i suoi dipendenti, ricambiando così la fiducia e laffetto che le avevano dimostrato stringendosi a lei nel momento del bisogno.
«Non è stato un compito facile - commenta limprenditrice - perché era venuto a mancare lunico riferimento sia per i dipendenti, sia per i fornitori e i clienti. Ma quando ho deciso di adottare un organigramma a piramide, inserendo nuovi quadri e dirigenti in varie posizioni chiave, ho apprezzato il fatto che la Simionato operasse da anni con un sistema qualità, che aveva contribuito a costruire dei percorsi ben definiti. A quel punto abbiamo cominciato a lavorare per obiettivi, responsabilizzando le persone nello svolgimento delle proprie attività ed è stato premiante per tutti».
Quando si intraprende un processo di revisione così profonda il coinvolgimento e la partecipazione delle persone sono infatti determinanti.
I cambiamenti hanno coinvolto naturalmente anche tutta la rete commerciale e di assistenza.
«Larea commerciale è stata potenziata. La direzione commerciale, che seguo personalmente, è ora affiancata da due area manager per lItalia e tre per lestero. Attualmente stiamo curando soprattutto i mercati europei, concentrando i nostri sforzi nella creazione di una nuova rete di agenti in grado di fornire anche unassistenza tecnica, in particolare per il nord Europa.
Per quanto riguarda il service, ora possiamo contare su quattro persone interne che gestiscono larea pezzi di ricambio, e su dieci tecnici dedicati allinstallazione e alla manutenzione. Non a caso, uno dei nostri principali obiettivi è quello di stipulare contratti in grado di assicurare al cliente unassistenza periodica e di ottimizzare al contempo il funzionamento delle linee in base al tipo di prodotto da confezionare.
In futuro, inoltre, grazie allo sviluppo dellelettronica, saremo anche in grado di avviare un servizio di teleassistenza».
Alla luce di questi profondi cambiamenti appare evidente che la Simionato non è più quella di una volta, e il mercato non tarderà ad accorgersi che lazienda - grazie alla nuova struttura e alla filosofia adottata - non solo è riuscita a creare innovazione di prodotto, ma è diventata più flessibile e affidabile, capace quindi di competere con le pressanti e attuali logiche di mercato.
|
 |
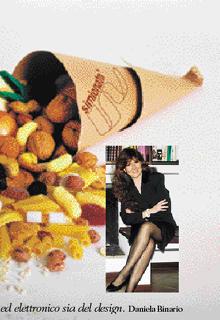
Total renewal
Simionato changes its skin and revamps. With the arrival of Patrizia Simionato, the company now has a new management and new market logic and aboveall a line of packaging machines new in terms of mechanics, electronics as well as design.
Daniela Binario
Often life puts capacity and strength to the test and reflecting on what has been done the results can be surprising.
The story behind Patrizia Simionato is an example of this. In October 2000 she made an important decision and accepted to take on the presidency of Simionato SpA, profoundly changing her life. It was not just a simple generational changeover, her entry into the company followed on from the sudden and painful loss of her father Paolo, company founder, and meant abandoning the activity that she had carried out for years as a consultant for the implementation of ISO 9000 systems and lecturer on the subject of quality.
Here attachment her family, her willpower and determination led her to accept the challenge and to concern herself with the company full time, trying herself out in a task that she had never carried out before, which meant sticking her neck out and going against everyone and everything.
The results went well beyond the rosiest of expectations, bringing the company based at Mestrino (Padua) - specialised in the construction of vertical and inclined packaging machines, linear and combination check-weighers, dosers, piece counters, weight control and product loading and transportation systems - to find new impulse and vigor.
Entering into the company - Patrizia Simionato confessed to us - meant continuing on with my fathers work, but the feeling and support offered to me by all the company staff were also decisive.
I also thought of all the other concerns that for some time and to varying degrees gravitated around Simionato and I decided to transform an extremely sad event into a moment of change and growth, this both for the company, as well as for the people who work in it. Changes have in fact been instituted and they have not only touched the administrative and commercial structure but have also led to the creation of an internal office for the electronic and engineering design. The result was first and foremost the devising of new electronics for all the machines, leading to the revision of production layout and, within a few months, the construction of new packaging lines that fully respond to the current needs of flexibility and reliability expressed by the market.
New electronics, new mechanics
As Patrizia told us - My father, even if he was not a technician and did not have at his disposal a structure dedicated to design inside the company (he drew to scale and built the relative models using Meccano), thanks to his inventive and intuitive capacities, he had always managed to create competitive products that found their placing in the mid to high range of the market.
This fact though did not make things easier for his daughter when she found herself administering the delicate phase of generational changeover: the resorting to external structures both for the engineering design as well as for making of the electronic boards to be assembled on the machine in fact had not created the ground for the fostering specific skills inside the company.
The first months of 2001 were the toughest - Patrizia told us - both for the trouble we had in getting hold of some components that we needed for assembling the boards vital for building the machines, also because in these cases the market tends to adopt a wait and see approach.
Fortunately in 1998, my father set up an internal structure for R&D for designing the machine electronics.
The results of this commitment became concrete in the year 2000, with a new electronics that allowed us to notably reduce the number of components, but aboveall apply a user interface that was the same for all the machines and, on top of that, tested to function in extreme use conditions (with working temperatures from between -10 and +70 °C). We are at any rate capable, in the event that it is required by the user, to integrate user interfaces bought on the market.
A good dose of courage was needed to take this first step and risk everything once again.
Time was scarce - Patrizia Simionato recalled - and I had to reorganise the company and the machines at the same time, thinking up a new product to win back shares of the market.
And we decided to do so creating an internal structure that, initially working with specialised external concerns, followingly allowed us to integrate the professional skills needed inside the company.
Rationalise the flows
In order to reduce time to market and to make the company more competitive the production layout has also been reorganised, and this has also led to a different assignment of tasks and responsibilities.
As Patrizia Simionato pointed out - We though it was more effective and advantageous to work on commission, producing preassembled machines in lots.
In this way, our people are not repetitively involved in the production of the same piece of equipment or single component, but work on the system seen as a whole, thus improving their own capacities.
The main advantage is that, looking after the setting up of the system and carrying out tests on the machine, all those involved in production, if need be, are also capable of carrying out technical assistance.
But not only this. Changing work methodology we can personalise the lines to an extreme, no small point, given that Simionato works broadly throughout the food sector, where needs vary a lot according to the segment (from pasta and confectionery to frozen foods, meat and vegetables, going on to products in powder and granule form).
Modifying the production layout has also meant adopting dynamic warehouse procedures capable of responding to new needs.
We tried to rationalise all the flow, on the one hand administering the inflow of raw materials and on the other the shipment of finished machines; we have also adopted a new administration system that enables the identification by way of a barcode of every piece in the warehouse.
Strength in personnel
Alongside the revision of the production side, Patrizia Simionato also found herself committed to the no less tricky task of reorganising personnel. On this count her capacity to look ahead, motivating and responsibilising her employees, thus returning the trust and affection they showed to her in her moment of need, was seen to be fundamental.
It was by no means an easy task - she goes on to say - because the sole point of reference for our employees, our suppliers and customers suddenly and simply just wasnt there anymore. But when I decided to adopt a pyramidal company organisation, inserting new middle management staff and managers in various key posts, I was able to appreciate the fact that Simionato had been working for years with a quality system, that had contributed to building up a well-traced out path. On this count we then began to work to set objectives, responsibilising the personnel in the carrying out of their specific tasks, a feature that has been good thing for everyone.
When a radically deep process of revision is adopted the involvement and the participation of the persons are in fact decisive.The changes naturally involved the entire commercial and assistance network.
The commercial area was strengthened. The commercial management, which I follow directly, is now flanked by two area managers for Italy and three for abroad. Currently we are aboveall looking after the European markets, concentrating our efforts in the creation of a new grid of agents capable of also supplying technical assistance, in particular for northern Europe.
As far as service is concerned, we can now count on four persons inside the company that run the spare parts area, and on ten technicians dedicated to installation and maintenance.
Not by chance, one or our main objectives is that of stipulating contracts capable of offering our clientele a periodic assistance and at the same time to optimise the functioning of the line on the basis of the type of product to be packed.
In future, as well as that, thanks to the development of electronics, we will also be able to start up a teleassistance service.
In the light of these profound changes it appears clear that Simionato is no longer the company it used to be, and the market will not be slow in noticing that - thanks to the new structure and philosophy adopted - it has not only managed to create product innovation, but that the concern has become more flexible and even more reliable, capable thus of competing with the pressing, current logic that rules the market.
|
|
Il frutto della ricerca
Gli obiettivi raggiunti dalla nuova Simionato non potevano che concretizzarsi positivamente sulle prestazioni degli impianti.
La nuova linea di macchine per il confezionamento Simpack, che viene presentata in anteprima a Interpack 2002, è stata progettata per rispondere a criteri di modularità, alta produttività, semplicità di gestione e manutenzione. In più, tutte le parti macchina sono state omologate per limmunità ai disturbi elettromagnetici con due classi superiori alle normative CE previste per luso industriale.
«La nuova gamma di confezionatrici verticali - precisa Patrizia Simionato - è diventata anche più flessibile perché siamo riusciti, grazie alla revisione del design, a ideare un involucro unico, sia nella configurazione per sacchetti piccoli che grandi. Questo consente di riconvertire la singola macchina in funzione delle diverse esigenze di produzione, semplicemente sostituendo il tubo formatore e le pinze di saldatura orizzontale e verticale (che sono due gruppi estremamente compatti).
Sempre per rispondere a criteri di flessibilità, abbiamo realizzato una confezionatrice inclinabile, che esponiamo a Düsseldorf. I modelli precedenti funzionavano con uninclinazione fissa di 45°, mentre ora, è possibile modificare linclinazione della macchina a seconda della fragilità del prodotto da confezionare, passando da un minimo di 25 a un massimo di 55°, senza lutilizzo di utensili e mantenendo fisso il punto di carico.
Unelettronica non comune
Abbiamo parlato di maggiori prestazioni dovute alla nuova elettronica, ma cerchiamo di capire perché limplementazione sulle nuove macchine contribuisce ad aumentare la competitività dellazienda di Mestrino. Progettando allinterno tutta lelettronica, hardware, firmware e software, e mettendo a punto i test sul prodotto (test sui circuiti stampati, sui singoli componenti montati e sullintera scheda in camera termica per 72 ore) la Simionato è riuscita a sviluppare in proprio il know how, offrendo così valore aggiunto e creando innovazione.
In passato venivano utilizzate ben 50 tipologie di schede, che combinate in modo differente, venivano applicate sui vari modelli. Oggi il numero delle schede è stato ridotto a 7, e i 4.000 componenti che servivano a realizzarle sono diventati 300. Ciò ha portato ad unestrema razionalizzazione del progetto e a un assemblaggio automatizzato; tale processo tra laltro, evitando la manipolazione delle schede da parte delloperatore, migliora laffidabilità del prodotto finale. In ogni caso, le migliori garanzie di qualità si devono anche alla particolare disposizione dei componenti sulle schede, che permette di ridurre le loro dimensioni e di diminuire notevolmente le temperature di esercizio, prolungando di conseguenza, grazie ai minori stress, la loro durata.
I vantaggi sono notevoli anche per il cliente perché, essendo neutre, le schede possono essere personalizzate (in base alla tipologia di macchina su cui vengono montate), tramite una microscheda denominata mediastick, che contiene il software applicativo e i parametri macchina necessari. Ma non è tutto. Nel caso un cliente disponga di più linee, invece di inserire sulle diverse macchine le singole ricette (passo di taglio, temperatura, ecc.), può servirsi del mediastick, spostando i parametri utili da ununità allaltra.
Non va dimenticato inoltre che, lelettronica sviluppata di recente consente di adottare uninterfaccia utente con prestazioni superiori rispetto a quelle disponibili in commercio: ha una protezione IP 65, è collocabile fino a una distanza di 15 m, ed è testata per operare in estreme condizioni di utilizzo (sulle macchine che lavorano nelle vicinanze dei forni piuttosto che nei pressi di celle frigorifere).
Proprio per garantire un funzionamento ottimale anche in ambienti difficili, il laboratorio è stato dotato di una camera climatica per test in estreme condizioni di umidità e temperatura, e di una serie completa di apparecchiature per i test di compatibilità elettromagnetica.
|
|
The fruit of research
The objectives attained by the new Simionato could not but positively affect the performance of their systems.
The new line of Simpack packaging machines, that will be presented in preview at Interpack 2002, has been designed in response to criteria of modularity, high productivity, being simple to run and to maintain. On top of this, all the machine parts have been type registered for immunity to electromagnetic disturbances two classes above that EC standards laid down for industrial usage.
The new range of vertical packaging machines - Patrizia Simionato states - has also become more flexible because we have managed, thanks to our redesign, to create a sole covering, both in the configuration for small as well as big bags. This allows one to reconvert the single machines according to the different production needs, simply substituting the forming tube and the horizontal and vertical seal pincers (that are two extremely compact units).
Still in response to flexibility criteria, we created an inclinable packer, that we will be shown at Düsseldorf. The preceding models worked with an inclination of 45°, while now the machine inclination can be modified depending on the fragility of the products to be packed, going from a minimum of 25° to a maximum of 55°, without the use of tools and keeping a set load point.
Out-of-the-ordinary electronics
We have spoken of a more powerful performance due to the new electronics, but we will try to understand why the implementation in the new machines contribute to increasing the competitivity of the Mestrino-based concern.
With the in-house design of all the electronics, hardware firmware and software, and devising the tests on the product (tests on printed circuits, on single components assembled and on the entire card in a heat chamber for 72 hours) Simionato has managed to develop its own knowhow, thus offering added value and creating innovation.
In the past as many as 50 types of cards were used, that combined in different fashions, were applied to the various models. Today the number of cards has been reduced to 7, and the 4,000 components needed to make them have now become 300. This has led to an extreme rationalisation of the project and to the automated assembly; among other things the said process improves the reliability of the end product by avoiding the manipulation of the cards by the operators. In any case, the best quality guarantees are also due to the special layout of the components on the cards, that enable reduced dimension of the card also allowing the reduction of working temperatures, consequently prolonging their lifespan thanks to the lesser stress.
The advantages are also considerable for the customer because, being neutral, the cards can be personalised (on the basis of the type of machine on which they are assembled) by way of a microcard called mediastick, that contains the applicative software and the necessary machine parameters. But this is not all.
In the event a customer has more than one line, instead of inserting the single formulas on the different machines (cutting rate, temperature etc), the mediastick can be used to shift the parameter from one unit to another.
Furthermore, it should not be forgotten that, the recently developed electronics enables the adopting of user interfaces with higher performances than those to be found on the market: with its IP 65 protection, the interface can be connected up at a distance of 15 m, and is tested for operating in extreme conditions of use (on machines that work near heat sources or close to freezer cells).
In order to also guarantee the optimum running in difficult conditions, the workshop has been fitted with a climatic chamber for tests in extreme humidity and temperature conditions, and a complete series of devices for testing electromagnetic capacities.
|
|
|
|
|
|
|
Da ditta individuale a S.p.A.
Le origini dellazienda veneta risalgono al 1963, anno in cui Paolo Simionato costruisce la prima confezionatrice per lazienda di famiglia Pastificio Simionato. Undici anni dopo, con la costituzione dellOfficina Meccanica Macchine Confezionatrici Simionato Paolo, inizia la produzione dei primi impianti di confezionamento, fino ad arrivare alla trasformazione, nel 1979, della ditta individuale in Simionato Elettronica S.r.l., e nel 1981 alla costruzione della prima pesatrice lineare elettronica.
Ma è tra il 1980 e il 1995 che lazienda conosce il periodo di maggiore sviluppo, favorito anche dallinnovazione apportata alle proprie macchine. È il caso delle pesatrici multitesta che, lanciate nel 1988, si sono presto affermate ponendosi in concorrenza con lofferta giapponese; ma non vanno dimenticate le confezionatrici verticali inclinate, ideate per trattare i prodotti delicati, sulla base di precise esigenze del mercato.
Negli ultimi due anni, inoltre, unaltra tappa importante riguarda la messa a punto della pesatrice multitesta inclinata per prodotti fragili, in cui la caduta del prodotto non avviene in verticale, da un cestello allaltro, bensì a spirale: in questo modo, si allunga il percorso e si riduce del 60-70% il rischio di rotture.
Nel 1999, inoltre, Paolo Simionato progetta un applicatore di zip per le confezionatrici verticali, che ha il grosso vantaggio di essere universale, e quindi in grado di lavorare indifferentemente con le più diverse tipologie di chiusura, dalle più piccole a quelle saldate su sacchetti più grandi, sia a cuscino che a fondo quadro. Ed eccoci al 2002: con la gestione di Patrizia Simionato nasce la nuova linea di confezionatrici verticali, progettata e sviluppata internamente, sia dal punto di vista elettronico che meccanico.
|
|
From individual concern to SpA
The origins of the Venetian company hark back to 1963, year in which Paolo Simionato built the first packaging machine for the Pastificio Simionato family pasta-making company. Eleven years on, with the setting up of the Officina Meccanica Macchine Confezionatrici Simionato Paolo [Paolo Simionato Packaging Machine Engineering Workshop], the production of the first packaging machines began, up to attaining the conversion in 1979, of the one-man company into Simionato Elettronica S.r.l., and in 1981 the building of the first linear electronic check-weigher.
But it was between 1980 and 1995 that the company really grew, favored also by the innovation undergone by its own machines.
This was the case with the multiheaded check-weigher that, launched in 1988, soon won a name for itself, competing with the Japanese product offering; yet we should not forget the inclined vertical packers, ideal for processing delicate products on the basis of the precise needs of the market. The last two years have seen important strides in the devising of inclined multiheaded check-weighers for fragile products, where the product does not fall vertically from one basket to another, but following a spiral: in this way, the path is lengthened and risk of breakage is reduced 60-70%.
In 1999 Paolo Simionato designed his zip applicator for vertical packers, that has the great advantage of being universal, and hence capable of working with the most different types of closure, from the smallest to that sealed to big bags, with pillow- and square-shaped bases.
And that brings us to 2002: with Patrizia Simionatos taking over the new line of vertical packers comes into being, with engineering and electronics entirely designed and developed in-house.
|
|
|
|
|