| | | | Geaf è fra le poche aziende europee specializzate nella produzione di macchine per la saldatura a radiofrequenza di materiali plastici, che trova largo impiego, fra laltro, nella produzione di blister, buste e astucci. Ma è anche un laboratorio autorizzato allo sviluppo in conto terzi di nuovi progetti e prodotti. Eccone i punti di forza, tecnici e commerciali. LG, EP | | 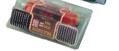 | | | | |  | | | I titoli sono di quelli che danno lustro: accanto alla certificazione ISO 9001, relativa allintero processo di progettazione e produzione, spicca la denominazione Laboratorio di Ricerca, sorta di patente rilasciata dallo Stato per sviluppare ufficialmente attività di ricerca sui vari aspetti della saldatura a radiofrequenza. È il fiore allocchiello della Geaf, che in questarea di attività ha totalizzato un gran numero di progetti andati a buon fine, talvolta anche con il supporto di finanziamenti pubblici. Ma non è solo una questione di prestigio e di business: in questo modo lazienda parmense alimenta e aggiorna la propria cultura tecnica, con ricadute positive anche sulla produzione a marchio proprio. «La nostra specialità - afferma al riguardo il sales manager della società, Maurizio Bardiani - sono le applicazioni industriali della radiofrequenza e della saldatura di materiali termoplastici, su cui sviluppiamo ricerche commissionate dallItalia e dallestero e che portiamo avanti fino alla fase di preindustrializzazione. Abbiamo lavorato per il settore automobilistico, nei casalinghi, nellimballaggio e tanti altri, sviluppando anche saldature a termocontatto per materiali alternativi al PVC (per esempio PP). Questo know how, unitamente a un approccio al mercato che prevede limmediata disponibilità delle macchine (complete di accessori) e alloriginale sistema di pianificazione produttiva, ci ha permesso di consolidare la presenza sui vari mercati, compensando le fluttuazioni nei singoli settori e conquistando nuovi spazi, magari anche a scapito dei concorrenti». Una tecnologia pulita Il generatore è un apparecchio che trasforma la normale tensione elettrica (3-400 V per 50 mHz) in una tensione anche cinque volte superiore, con una frequenza che raggiunge i 27 mHz. In questo modo, e applicando una pressione, si ottiene la fusione dei materiali e la loro conseguente saldatura. «A differenza di altre tecnologie che si basano sul calore, però - precisa Bardiani - la saldatura a radiofrequenza (definita anche ad alta frequenza) non genera fumi, perché linnalzamento di temperatura non avviene per trasferimento di calore ma a seguito di unagitazione molecolare indotta dallazione simultanea della pressione e del campo elettromagnetico. Si tratta di un risvolto interessante sul piano della sicurezza delloperatore e dellambiente di lavoro, a cui si aggiunge il vantaggio della semplicità». I materiali che si possono saldare con questa tecnica sono soprattutto il PVC flessibile o rigido, lEVA (etil-vinil-acetato) e varie poliolefine composte da polietileni a cui vengono aggiunte parti di EVA proprio per consentirne la saldabilità. Non sono possibili, se non in casi particolari, saldature ad alta frequenza di elementi rigidi: i materiali devono presentarsi in fogli più o meno flessibili, con spessori nellordine di qualche decimo (1 mm max). I settori che adottano normalmente lalta frequenza sono molti e comprendono lautomobilistico, dove viene impiegata nella produzione di componenti interni (pannelli porta, tappeti, alette parasole e rivestimenti vari...), il medicale, per sacche monouso, limballaggio, dove spiccano i blister, la prima infanzia (parti di carrozzine, passeggini ecc.) e le grandi coperture (dalle tensostrutture ai più piccoli teloni per le coperture dei camion). Dal generatore alla soluzione completa Data la relativa semplicità di utilizzo della tecnologia, nella saldatura a radiofrequenza contano in maniera particolare altri aspetti del business. Lo testimonia limportanza che riveste, nella success story della Geaf, la capacità di cogliere le esigenze del mercato e di assecondarle. «In Francia - esemplifica Bardiani - un distributore particolarmente sensibile ci ha incoraggiati a lavorare sugli aspetti che influiscono sulla velocità del cambio stampi e del controllo di processo. Grazie a questi progressi, in questarea siamo diventati i fornitori leader del segmento blisteratura, con un market share prossimo al 50%. E il risultato è tanto più significativo visto che, qui, lenorme sviluppo delle superfici di vendita a libero servizio ha trainato la diffusione del blister (confezione essenziale da appendere, in cui si mette di tutto, dal pallone al volante), e la realizzazione, quindi, di macchine particolarmente efficienti e versatili. La natura della prestazione richiesta, naturalmente, varia a seconda del tipo di utilizzatore: i produttori di beni che realizzano la blisteratura in proprio, a fine linea, di norma non effettuano molti cambi formato ma poche operazioni ripetitive; viceversa, per i terzisti che lavorano quotidianamente (e freneticamente) su una gran varietà di prodotti diversi, velocità e facilità del cambio stampo sono vitali. Stimolati dai clienti stessi abbiamo quindi messo a punto sistemi automatici di centratura e una modalità di cambio che non richiede utensili, grazie a cui lo stampo si sblocca semplicemente azionando una leva. E ora stiamo lavorando a soluzioni che rendano meno faticosa anche la successiva operazione di rimozione dello stesso». Le macchine della Geaf sono in grado di realizzare sia la tradizionale saldatura a radiofrequenza (di un film di PVC con un film di PVC) sia quella su un blister con la base di cartone. Analoghe problematiche interessano gli altri due grandi sbocchi nel packaging, in cui lazienda parmense registra incrementi lievi ma costanti: la realizzazione delle grandi borse con cerniera e maniglia per le coperte o i set di lenzuola, e la produzione di astucci di plastica - per esempio, dove si confezionano i costumi da bagno, lintimo o i profumi - che richiedono, prima di essere avviati alla piega-incolla, una sorta di pre-fustellatura realizzata sulle macchine Geaf («Forniamo i più grandi converter europei»). Lorganizzazione del lavoro Naturalmente, commenta Bardiani, la bravura - e la fortuna - sta anche nel capire quali suggestioni seguire. «Già 15 anni fa sembrava che il film di polipropilene dovesse soppiantare il film di PVC in molte applicazioni industriali, mentre in realtà, non è accaduto e, nelle applicazioni che ci riguardano, il PVC ha mantenuto le sue quote di mercato. Diverso è il caso del PETG, per cui abbiamo sviluppato una tecnologia di saldatura ad hoc, che può essere realizzata sui nostri impianti tradizionali con accessori dedicati». Ma il mercato non chiede solo macchine efficienti e dedicate: risulta, infatti, particolarmente sentita lesigenza di abbreviare i tempi di consegna. È proprio per incontrare questa richiesta che Geaf si è dotata di un efficiente sistema di gestione delle informazioni, su cui basa piani di produzione periodici, in modo da disporre sempre a magazzino di macchine pronte o, quantomeno, di tutti i componenti necessari per assemblarle velocemente. In sintesi, si tratta di un sistema di archiviazione dei dati relativi alle macchine realizzate, compresi la tipologia di cliente e di problema risolto. Su questo prezioso patrimonio di conoscenze, si basa poi la pianificazione produttiva che, a dispetto dei possibili rischi (nessun calcolo, per quanto complesso, garantirà la vendita delle macchine già realizzate) è stato uno degli aspetti vincenti della strategia Geaf. La riprova? «Nel campo della blisteratura - esemplifica Bardiani - lesigenza di disporre della macchina in tempi brevi è così sentita da portare, in alcuni casi, anche allacquisto di un modello non perfettamente in linea con le necessità del momento, purché pronto». La produzione standard, dunque, in molti casi rappresenta lasso nella manica della società che, infatti, le ha dedicato il secondo stabilimento di Marano. E le personalizzazioni? «La nostra gamma di macchine è così ampia che in genere soddisfa le richieste del mercato, mentre le personalizzazioni riguardano perlopiù la lingua delle istruzioni a display e pochi altri dettagli della medesima portata. Lintervento creativo, casomai, lo facciamo a monte, quando il cliente ci sottopone un problema inedito, che mette alla prova la competenza e la fantasia dei nostri tecnici. Che non temono le sfide». |  | Radiofrequency? An enterprise! Geaf is one of the few European companies that specialises in the production of machines for radiofrequency welding of plastic materials, which are also widely used in the production of blister packs, bags and cases. Geaf is also a laboratory which conducts third-party development of new projects and products. A company with well-founded strengths in both the commercial and technical sides. Titles of distinction: in addition to ISO 9001 certification, the entire design and production process carries the Research Laboratory title, a government-issued category of licence to officially develop research activity on various aspects of radiofrequency welding. This is the jewel in the crown for Geaf, who have completed a large number of effectively operative projects, some of which have been supported by public funds. However, this is not merely a question of prestige and business: this allows the company to foster and continually up-date its technical knowhow, with positive spin-offs on their own brand production as well. «Our speciality states Maurizio Bardiani, company sales manager lies in industrial applications of radiofrequency and welding of thermoplastic materials, where we conduct Italian- and foreign-commissioned research and then develop these up to the pre-industrialisation stage. We have worked for the automobile, domestic, packaging and many other sectors, and also developed thermocontact welding for PVC-substitute materials (e.g. PP). It is this knowhow, together with a market approach that provides for immediate machine availability (complete with accessories) and our original production planning system, that has allowed us to consolidate our presence on various markets, compensating the fluctuations in individual sectors and gaining new shares, maybe even to the cost of other competitors». A clean technology The generator is a piece of equipment that boosts normal electric tension (3-400 V per 50 MHz) to even five times its original value, with a frequency that reaches 27 MHz. By utilising this and applying pressure, the materials melt and are then welded. «However, unlike other technologies that are heat-transfer-based Bardiani explains radiofrequency welding (also defined as high-frequency welding) does not use heat to raise the temperature, and so does not generate any fumes. The rise in temperature is achieved through molecular agitation induced by both pressure and electromagnetic field. This leads to interesting implications for operator and work environment safety, with the added advantage of simplicity». The materials that can be welded with this system are mainly flexible or stiff PVC, EVA (ethyl-vinyl-acetate) and various polyolefinics composed of polyethylenes to which a portion of EVA is added to make these weldable . Except for particular cases, it is not possible to weld rigid elements: the materials must be in a sheet form that has a certain degree of flexibility, with a thickness within the range of a few tenths (max. 1mm). There are many sectors that use high frequency, including automobile production, where it is used for producing interior components (door panels, foot mats, sunscreens and various different coverings...), medicines, for mono-use sacks, packaging, especially for blister packs, childcare accessories (parts of prams, buggies etc...) and large coverings (from stretched flexible structures to truck coverings). From the generator to the complete solution Given the relative simplicity of use of the technology, other aspects of the business are particularly important in the radiofrequency welding sector. In the Geaf success story, this can be seen in the importance given to the ability to comprehend market requirements and serve these. «in France Bardiani cites an example a particularly sensitive distributor encouraged us to work on the features that influence the speed of mould-change and process control. Thanks to the progress made here, we have become the leading supplier in the blistering segment in this area, with a market share close to 50%. And the result is even more significant, seeing that the huge development in self-service sales areas has been responsible for the popularity of blister packs (easy to hang packages, which can contain everything, from a football to a steering wheel), and hence the creation of machines that are highly efficient and versatile. Naturally, the nature of performance required varies according to the type of user: producers of goods that make their own, end-of-line, blister packs, generally use a small number of repetitive operations rather than many format changes; on the contrary, speed and ease of format change are vital for third party producers, that work daily (and at a frenetic pace) on a large selection of different products. And so we were stimulated by our customers to develop automatic matching systems and a format change mode that does not require tools, whereby molding is stopped automatically by using a lever. We have now moved onto working on solutions that make mold removal an easier operation. Geaf machines are capable of traditional radiofrequency welding (of a PVC film with a PVC film), as well as blister welding with a cardboard base. The Parma company is finding similar issues in the other two large packaging market outlets, where they are recording slight but constant growth: production of large zipped bags with handles for blankets or sets of sheets, and the production of plastic boxes such as for packaging bathing costumes, underwear or perfumes. These first of all require to be set up for fold and glue, a type of pre-die-cutting done on Geaf machines («we supply the largest European converters»). Organisation of the work Bardiani comments that naturally the expertise and luck also lies in knowing which suggestions to follow. «As many as 15 years ago it seemed that polypropylene films were to replace PVC film in a large number of manufacturing applications, whereas this did not actually happen, and PVC has retained its market share in the applications that we deal with. This is not the case with PETG, for which we developed an ad hoc welding technology that can be done on our traditional systems with the aid of special accessories». But the market demands more than just efficient and purpose-designed machines: there is a definite demand for the reduction of delivery times. And so Geaf has moved to respond to this demand by employing an efficient information management system, which provides them with a base for periodical production programmes so that the company is capable of providing the warehouse with ready-to-go machines or, at least, with all the components necessary for a speedy assembly. This is essentially an archive system of all the data relating to produced machines, including customer category and the problem solved. This valuable information tool then provides the base for production planning, despite possible risks (no calculation, no matter how complex it is, will guarantee that machines that have already been produced will sell), has been one of Geafs winning tools. Proof? «In the blistering field Bardiani provides an example there is such a need to have the machine as soon as possible that, in some cases, a model that does not respond fully to the requirements of the moment will be bought as long as it is ready at that time». Therefore, it is often the case that the companys backbone lies in their standard production, for which they have allocated the second plant at Marano. And personalisation? «Our range of machines is so wide that it generally satisfies market demands, while the majority of our personalised features are accounted for by the language of the display instructions and a small number of other similarly significant details. Any creative interventions are done at source, when the customer poses a problem we have not previously encountered, and puts the skill and imagination of our engineers to the test. Our technical people have no fear of challenge». | | | | Un milanese a Parma Che cosa fa un milanese a Parma (più precisamente a Calestano), nel 1971, con il gusto del nuovo e tanta intelligenza imprenditoriale? Fonda una propria azienda nel campo della saldatura a radiofrequenza e la chiama Geaf; poi la consolida, fino a farne in una decina danni unimpresa strutturata per servire i settori automobilistico, medicale, prima infanzia, delle grandi coperture e dellimballaggio (che rappresenta il 20% circa del fatturato complessivo). Limprenditore si chiama Antonio Fabiano e la Geaf oggi è una realtà da 15 miliardi, con un secondo stabilimento di 800 m2 a Marano, dedicato alla produzione di macchine standard, e 65 dipendenti di cui 15 esclusivamente focalizzati sulla progettazione meccanica, elettronica e dei generatori a radiofrequenza. Certificata ISO 9001, Geaf è oggi anche ufficialmente riconosciuta dallo Stato come Laboratorio di Ricerca che sviluppa, su commissione di aziende italiane e straniere, prodotti basati sulla saldatura a radiofrequenza. Nellimballaggio, questa tecnologia si utilizza primariamente per la saldatura di blister di PVC o PETG - perlopiù a doppio guscio, o a un guscio con foglio di PVC sul retro - per la realizzazione di astucci di PVC, PET amorfo o PETG, e per la produzione di varie tipologie di borse trasparenti di plastica, per il confezionamento di biancheria da casa. Geaf oggi esporta circa il 60% della propria produzione (è una quota in progressiva e costante crescita), perlopiù in Europa dove vanta - nel segmento blister - la leadership sul mercato francese. | | A Milanese in Parma What was a Milanese man doing in Parma (Calestano to be precise) in 1971 with a taste for innovation and a lot of entrepreneur acumen? He set up his own company in the field of radiofrequency welding and he called it Geaf; then he consolidated the company to such an extent that in just ten years it was an enterprise structured to serve the sectors covering the automobile, medicinal, childcare, large coverings and packaging (which accounts for approx. 20% of total turnover) industries. The entrepreneur is called Antonio Fabiano, and today Geaf is a 15-billion-lire activity, with a second, 800 m2 plant in Marano for the production of standard machines, employing 65 people, 15 of whom work exclusively on the mechanical and electronic design of radiofrequency generators. Geaf is ISO 9001 certified, and is also officially recognised by the Italian State as a Research Laboratory that conducts commissioned (by both Italian and non-Italian firms) development of products based on radiofrequency welding. In the packaging sector, this technology is used predominantly for welding PVC or PETG blister packs most of which are double shell, or single shell with PVC-sheet backing for producing PVC boxes, amorphous PET or PETG, and the production of various types of transparent plastic bags, and for packaging household linen. Approximately 60% of Geaf production is exported (and this share is constantly rising) mainly to Europe, where in France it is number one in the blister segment. | | |  | | |