| | |  | 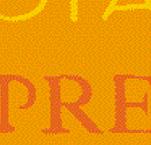 | | Schiavi ha presentato una nuova rotocalco da 500 m/min che, a fine lavoro, consente il lavaggio integrato in macchina dellintero gruppo di inchiostrazione e la sostituzione in automatico dei cilindri. E che permette di utilizzare nel modo migliore anche le più leggere e flessibili sleeve. Stefano Lavorini | |  | | | Gli ordini si accorciano e la roto accelera i tempi, mostrando, a dispetto dei più pessimisti, di saper recuperare la distanza che, fin qui, si è andata creando, in materia di flessibilità ed economicità, rispetto alla flexo. Schiavi, nome di spicco nel panorama italiano dei costruttori delle macchine da stampa rotocalco e flessografiche, compie infatti un ulteriore, importante, passo in avanti presentando una nuova roto a elevate prestazioni con lavaggio integrato del gruppo di inchiostrazione in macchina e cambio simultaneo in automatico di tutti i cilindri. Sviluppando le esperienze maturate con la serie di rotocalco Idea - realizzata in collaborazione con lazienda tedesca Transfertex - la società piacentina può offrire oggi anche la SG 2000 che, nuova in tutto e per tutto, rappresenta unalternativa soprattutto in termini di prestazioni - la velocità passa da 250 a circa 500 m/min (ma con adeguate camere di essiccazione si può arrivare anche a 700 m/min) - ed efficienza. Il risultato finale è una macchina flessibile e facile da condurre, in grado di assicurare evidenti ritorni economici, soprattutto in caso di tirature brevi, e che permette, per bontà di progetto, di sfruttare appieno, in alternativa ai cilindri tradizionali, le potenzialità offerte dalle sleeve. Tempi corti per la roto Il settore degli imballaggi flessibili è caratterizzato da anni da una progressiva riduzione della tiratura per singolo ordine. Il mercato continua a crescere, ma è sempre più segmentato e questo impone macchine in grado di assicurare cambi lavoro sempre più rapidi e efficienti. «Già oggi - spiega Marco Curtoni, Product Development Director della Schiavi - le attuali macchine da stampa rotocalco sono dotate di carrelli intercambiabili che permettono, nel caso, ad esempio, di una linea a 7 colori, di passare da un lavoro ad un altro in circa 45 minuti. Il problema vero, in questi casi, non è tanto nei tempi di set-up, ma nella gestione dei flussi e dei tempi relativi al lavaggio fuori linea dei carrelli. Di fatto, in funzione dei lotti reali di produzione - in unora, mediamente, si stampa un ordine di 10.000 metri - è difficile provvedere, in questo lasso di tempo, alla pulizia e allattrezzaggio di tutti i carrelli necessari per avviare un nuovo lavoro. Ciò si traduce in un aumento degli investimenti in attrezzature complementari alla macchina da stampa (cresce il numero dei carrelli) e un significativo aggravio in termini di costi di manodopera, in quanto sono necessarie almeno tre persone per turno che provvedano al lavaggio e alla movimentazione di queste attrezzature di supporto». Per dare soluzione a questi problemi, la Schiavi ha realizzato una nuova macchina, che permette, in meno di un quarto dora, di passare dallultimo metro di stampa di un lavoro, al primo metro di quello successivo. Una macchina pulita, dentro e fuori «La SG 2000 - sottolinea Curtoni - è stata progettata ex novo, sulla scorta delle esperienze fatte con la rotativa Idea, utilizzando i brevetti di base, ulteriormente sviluppati per raggiungere le alte velocità. Come per la Idea, la nuova macchina è dotata di un sistema per il lavaggio integrato degli elementi, costituito da un insieme di ugelli spruzzatori, opportunamente posizionati e alimentati automaticamente, che garantiscono la pulizia del sistema di inchiostrazione, della racla, e del cilindro stampa. Sono necessari circa 7 litri di solvente per ogni elemento stampa, che vengono successivamente recuperati tramite distillatore. Il lavaggio integrato in macchina permette di effettuare la pulizia dei cilindri immediatamente dopo larresto della linea, quando linchiostro è umido, azzerando il traffico di carrelli intercambiabili, sporchi, allinterno dello stabilimento. La movimentazione dei cilindri nel caso della SG 2000 viene effettuata mediante carrelli-navetta semplici e pratici che, senza alcuna motorizzazione, consentono di effettuare loperazione di sostituzione automatica e contemporanea dei cilindri di stampa su tutti gli elementi, con conseguente drastica riduzione del tempo di fermo macchina. La SG 2000 è inoltre dotata di racla con preset automatico, regolato tramite computer che fa sì che il gruppo si allontani automaticamente durante loperazione di cambio cilindri, per poi riposizionarsi, sempre in automatico, a operazione ultimata». Un carrello semplice semplice Alla flessibilità di gestione fa da contrappunto la semplicità delle singole soluzioni tecniche. Di rilievo il nuovo carrello portacilindri (brevettato), che contribuisce a snellire e velocizzare i cambi di commessa. «Questo mezzo - specifica Curtoni - è stato ideato e sviluppato dallo stampatore tedesco Transfertex e il suo funzionamento è tanto semplice quanto efficace. Il carrello, caricato con il cilindro nuovo, viene inserito nella linea mentre questa è in funzione. Terminato il lavoro, a macchina ferma e dopo il lavaggio, il cilindro da sostituire viene automaticamente espulso dallelemento di stampa e fatto rotolare, per gravità, sul carrello, previa apertura dei blocchi di serraggio dei perni mentre, in contemporanea, il nuovo cilindro rotola e si posizione automaticamente nelle sedi dellelemento stampa. Il tutto senza motorizzazioni, né intervento delloperatore». Cilindri o sleeve, a piacimento La rotocalco SG 2000 nasce con lobiettivo di offrire ai converter il meglio della tecnologia e si propone, nelle intenzioni del costruttore, di rappresentare lo stato dellarte del settore anche per quanto riguarda la possibilità di utilizzare, con pari efficienza ed efficacia, sia i cilindri tradizionali sia i cilindri leggeri (sleeve). «I nuovi elementi di stampa, dotati di motorizzazione indipendente, spiega Marco Curtoni sono stati progettati per consentire la sostituzione rapida in macchina del carrier e/o della sleeve rotocalco senza rimuovere lalbero». Loperazione che viene svolta in automatico, dopo il ciclo di lavaggio integrato del gruppo di inchiostrazione, è estremamente semplice: - posizionamento verso lalto dellattacco per laria compressa ricavato sullalbero; - sblocco e allontanamento del supporto dellalbero del cilindro, lato operatore, e contemporaneo posizionamento, sullestremità opposta, di un controsupporto; - connessione dellerogatore di aria compressa (sono necessarie circa 20 bar di pressione); - rimozione e montaggio manuale del carrier e/o della sleeve attraverso lapertura ricavata, lato operatore, nella spalla di ogni elemento stampa; - ripristino delle condizioni operative. Secondo Curtoni lutilizzo delle sleeve sulla SG 2000 offre notevoli vantaggi in quanto permette di coniugare flessibilità e leggerezza delle matrici con i punti di forza peculiari della rotocalco, primo fra tutti, la ripetitività in termini qualitativi del processo di stampa e la possibilità di effettuare in linea tutte le lavorazioni accessorie (laccatura, applicazione a registro di cold-seal, accoppiamento, ecc.). Fuori dai luoghi comuni La Schiavi con questultima macchina ha dimostrato di avere ancora ben vivo il senso della sfida e di credere nella possibilità di perfezionare significativamente le proprie proposte, offrendo sempre e comunque qualcosa di economicamente competitivo. «La SG 2000 comporta un investimento un po più elevato rispetto a quello di una rotocalco normale, ma genera risparmi considerevoli a vari livelli: si pensi anche solo alla riduzione di personale, alle economie che derivano dallabbattimento dei tempi di cambio formato, allaumento di produttività e, nel caso di utilizzo delle sleeve, al minor costo di acquisto e di gestione di queste matrici rispetto ai cilindri tradizionali». E il mercato oggi sembrerebbe pronto a cambiare, soprattutto alla luce di quanto emerso durante lultima Drupa: «Dopo una crescita impetuosa sia di tecnologia che di vendite, la flessografia sta ormai raggiungendo i suoi limiti fisiologici», sostiene Curtoni. «Col senno di poi, possiamo inoltre valutare che il suo sviluppo sia andato a scapito più delloffset che della roto, che resta più semplice da usare e garantisce una produttività e uno standard qualitativo, per quanto riguarda la stampa, indubbiamente superiore. Il contesto è dunque incoraggiante anche per la tecnologia rotocalco, che mostra una rinnovata vitalità». La SG 2000 della Schiavi promette molto e, probabilmente, se tutto funzionerà a dovere, si dovranno rivedere completamente i parametri di convenienza nel settore del flexible packaging, ora che con questo modello si possono gestire con efficienza e redditività sia ordini lunghi che brevi. Questo modello ha già avuto la preferenza di un grande trasformatore europeo. |  | Better than a rotogravure printing press Schiavi has presented a new 500 m/min rotogravure printing machine that performs integrated washing of the machine and the entire inking unit at the end of the work run, along with the automatic substitution of cylinders, enabling optimum use of even the most flexible of sleeves. Orders are getting shorter and rotogravure is speeding up, this despite the pronouncements of the most convinced pessimists, showing that rotogravure has been able to bridge the hitherto widening gap between itself and flexo printing in terms of flexibility and cost effectiveness. Schiavi, leading name in the Italian world of rotogravure and flexographic print machines, has made another further important step forward, presenting a new high performance rotogravure press with integrated washing of the inking unit in the machine and simultaneous automatic change of all the cylinders. Working on experience drawn from Idea rotogravure series - made in cooperation with the German company Transfertex - the Piacenza-based company is now also offering the SG 2000, new in all its features, that stands as an alternative aboveall in terms of performance - speed going from 250 to around 500 m/min (but with adequate drying chambers 700 m/min can be obtained) - and efficiency. The end result is a flexible machine that is easy to run, capable of ensuring considerable economic returns - aboveall on short runs - and that thanks to its design, enables the potentialities offered by sleeves to be exploited to the full, this as an alternative to traditional cylinders. Short times for the gravure press The flexible packaging sector has for years now featured a progressive reduction of runs for single orders. The market continues to grow, but is becoming evermore segmented and this imposes the need for machines that are even more capable of ensuring even faster and more efficient work changes. As Marco Curtoni, Product Development Director of Schiavi explains - «The current rotogravure presses have interchangeable trolleys that for example in the case of a 7 color line allow one to go from one job to another in the space of around 45 minutes. Here the real problem does not so much lie with setting up, but in administering trolley flows and the wash times out of line. In fact, seeing things in terms of actual production lots - on average in an hour 10,000 metres are printed - it is difficult to see to the cleaning and tooling up of all the trolleys needed to start up a new job in this lapse of time. This leads to increased investments in equipment complimentary to the print machines (entailing an increase in the number of trolleys) also upping workforce costs, in that one needs at least three people per shift to see to the washing and transferring of the ancillary equipment». To solve this problem Schiavi has come up with a new machine that allows you to go from the last metre of print in one job to the first metre of the following job in under a quarter of an hour. A clean machine inside and outside «The SG 2000 - Curtoni underlines - has been designed from scratch, drawing on experience gained with the Idea rotogravure press, using the basic patents that have been further developed to attain the high speeds. As with Idea the new machine is fitted with an integrated washing system comprising a group of strategically positioned automatic feed spray nozzles that guarantee the cleaning of the ink system, the doctor blade and the print cylinder. Some 7 litres of solvents are needed for each print unit; these are subsequently recovered by a distiller. The on-board integrated washing enables the immediate cleaning of the cylinders after line stops when the ink is still moist, eliminating the toing and froing of dirty interchangeable trolleys inside the works. With the SG 2000 cylinder shifting is performed by simple and practical shuttle trolleys, that enables an automatic simultaneous substitution of print cylinders on all units without using motors, consequently drastically cutting machine down time. The SG 2000 also has a computer controlled doctor blade with automatic preset: the unit is automatically withdrawn during the cylinder change operations and automatically repositioned once the operation has been completed». A simple trolley High running flexibility goes hand in hand with the simplicity of the single technical solutions. Worthy of note the new patented cylinder-bearing trolley that contributes to reducing and speeding up job change operations. As Curtoni explains «this vehicle, devised and developed by the German print firm Transfertex operates in a simple and effective manner. The trolley, loaded with the new cylinder, is inserted in the line while this is operational. Once work is over, with the machine at a standstill and after washing, the cylinder to be substituted is automatically expelled from the print device and rolled onto the trolley by force of gravity - this after the pin clamps have been opened. At the same time the new cylinder is rolled down to automatically position itself in the berth of the print unit. All this without motors or operator intervention». Cylinder or sleeve as desired The SG 2000 rotogravure press was created to offer the converter the best in technology and in the builders intentions is set to represent the state-of-the-art in the sector, this both using traditional as well as light cylinders (sleeves), offering equal efficiency and effectiveness with both solutions. As Marco Curtoni explains «The new print units with independent motors have been designed to enable the rapid substitution in the machine of the carrier and/or rotogravure sleeve without removing the shaft». The operation, that is carried out automatically after the integrated washing cycle of the ink unit is extremely simple and entails the: - upward positioning of the compressed air socket on the shaft; - unclamping and removal of the shaft support of the cylinder on the operators side and simultaneous positioning of a counter support on the opposing side; - connecting up of the compressed air dispenser (around 20 bars of pressure needed); - manual removal and assembly of the carrier and/or the sleeve through the opening on the operators side situated in the shoulder of every print unit; - reinstating of operating conditions. According to Curtoni the use of the sleeve on the SG 2000 offers notable advantages in that it allows one to marry flexibility and lightness of the matrixes with the special strongpoints of rotogravure: first and foremost qualitative repetitivity of the print process and the possibility of carrying out all ancillary operations in line (lacquering, registered application of cold-seal, coupling, etc.). Beyond the cliché With its latest machine Schiavi has once again shown itself capable of rising to a challenge along with confidence in being able to perfect its own proposals, at any rate showing they are always capable of coming up with something that is economically competitive. «The SG 2000 entails an investment a bit higher compared to that of normal gravure machines, however this is offset by the considerable savings it generates on various levels: one only has to think of the reduction in personnel, of the savings that come from the reduction of format changes, the increase in productivity, and in the case of the use of the sleeve, of the lesser purchase and running costs of the same compared to traditional cylinders». And the market now ready for the change, aboveall in the light of what emerged at the last Drupa. As Curtoni sustains: «After an impetuous growth involving both technology and sales flexography is now reaching the physiological limits of its expansion. With hindsight we can also now see that its growth has encroached more on offset rather than on the rotogravure printer, the latter still being simpler to use while guaranteeing undoubtedly higher productivity and quality standards as far as print is concerned. The context is also hence encouraging for rotogravure technology that is showing a renewed vitality». Schiavis SG 2000 promises a lot and probably, if it functions as laid down, one will have to completely overhaul the cost-effectiveness parameters of the flexible packaging sector, now that with this model the profitability and the efficiency of both long and short orders can be handled. The model has already won over a large European converter. | | | | Levoluzione prende il volo La rotocalco SG 2000 è un prodotto alto di gamma, che si propone di coniugare produttività e flessibilità per offrire nuove ragioni di convenienza agli utilizzatori. Per raggiungere questo obiettivo la Schiavi ha previsto fin dalle prime fasi di studio la possibilità di utilizzare, in alternativa ai cilindri tradizionali, le matrici leggere, che acquisteranno in futuro sempre più importanza. A garanzia di migliori risultati, il progetto ha visto - tra gli altri - il coinvolgimento di Rotoincisa, realtà italiana a cui in buona parte si deve la diffusione a livello internazionale del sistema delle sleeve rotocalco. Il risultato più evidente di questa partnership è stata la messa a punto, in occasione della Drupa, di un carrier (adattatore) per molti versi paragonabile a quello utilizzato nella stampa flexo. «Si tratta - spiega Laura Teresa Venturati, titolare dellazienda di Rho - di corpi intermedi di diverso sviluppo, che vengono montati tra lalbero e la sleeve. Il loro contributo in termini di maggior flessibilità è determinante, perché permettono al converter di ridurre drasticamente linvestimento in cilindri aria (il cilindro madre su cui viene calzata la sleeve, ndr.), e di realizzare il sogno degli stampatori rotocalco: il cambio lavoro in pochi secondi, direttamente in macchina da stampa, anche nel caso di utilizzo di differenti sviluppi. In termini generali, non va poi trascurato che una copper sleeve depellicolabile, ovvero che può essere incisa più volte, costa circa il 50% in meno di un cilindro tradizionale. Il sistema, da tempo consolidato, si sta sempre più diffondendo e per favorire questa dinamica, la società Rotoincisa sta realizzando cessioni di know-how ad altre realtà di settore, in considerazione del fatto che le innovative cooper sleeve, non avendo più il corpo in nichel, possono essere prodotte in fotoincisione, stravolgendo così le tradizionali logiche produttive. | | The evolution takes off The SG 2000 rotogravure printing press is a top notch product born out of the intent to combine productivity and flexibility in a drive to offer ever greater price convenience to the user. In order to attain this objective, right from the first study phases Schiavi envisaged the possibility of using light matrixes as an alternative to traditional cylinders, a feature sure to acquire ever greater importance in the future. To guarantee the best results the project has witnessed among others the involvement of Rotoincisa, the Italian concern that has to a greater extent contributed to the spread of the rotogravure sleeve system internationally. The most evident result of this partnership has been the devising for Drupa of a carrier (adapter) that in many features can be compared to that used in flexo printing. As Laura Teresa Venturati, owner of the firm based at Rho near Milan explains «We are here speaking of intermediate bodies fitted between the shaft and the sleeve developed in a variety of ways. Their contribution in terms of greater flexibility is strategic, because they allow converters to drastically reduce investments in air cylinders (the parent cylinder over which the sleeve is fitted E.n.), and have made the rotogravure printers dream come true: workchanges in just a few seconds, directly in the printing press even with different developments. In general terms one should not overlook the fact that a copper sleeve from which the film can be peeled away - rather meaning it can be engraved several times - has a cost standing at around 50% of a traditional cylinder. The use of this system, that has been undergoing consolidation some time now, is spreading rapidly. In order to further the process Rotoincisa is releasing knowhow to other concerns in the sector, this in consideration of the fact that the innovatory copper sleeves, no longer having a nickel body, can be produced using photoengraving, thus revolutionising the traditional logic of production. | | |  | | |