Film flessibili, residuo solvente e valore di un comparto

Cronaca della tavola rotonda promossa dal Giflex: trasformatori ed end user del settore alimentare si sono trovati a discutere di residuo solvente nell'imballaggio flessibile.
Dalla valutazione sulle metodologie seguite per determinare l'accettabilità delle soglie
di percezione di acetato di etile, nonché la sua reale incidenza sulle proprietà organolettiche degli alimenti, si è presto passati a considerare le molte altre variabili in gioco,
tra cui il problema più generale dellodore degli imballaggi. A tutto vantaggio di un sapere (e di un bene) comune. Luciana Guidotti, Stefano Lavorini
Sulla base dei risultati emersi nel corso dello studio effettuato da PDC, e culminato nella pubblicazione del Quaderno tecnico "La stampa rotocalco di film flessibili e il problema dei solventi residui" (*), Giflex (il gruppo di lavoro che fa capo ad Assografici e che rappresenta circa l'80% dell'attività di trasformazione italiana) sta lavorando alle revisione delle specifiche tecniche che sono parte integrante dei capitolati di fornitura. Nel frattempo promuove occasioni di dibattito, chiamando per ora in causa i grandi utilizzatori italiani e stranieri di imballaggio flessibile, ma prospettando già ulteriori iniziative allargate a produttori di materie prime e agli operatori della distribuzione.
Da parte sua, Giflex, mette sul tavolo conoscenze certe e accertate in merito alle problematiche più spinose che "segnano" l'attività del converting nazionale, invitando fornitori e clienti a esprimersi liberamente, in un onesto gioco di botta e risposta, che non può che risultare vantaggioso per tutti.
Questa scelta si è concretizzato anche in occasione dellincontro svoltosi a ottobre presso Villa Torretta, alle porte di Milano, ed è tutto nellesortazione che Ruggero Gerosa, presidente Giflex, ha rivolto ai partecipanti affinché "si realizzi un confronto aperto fra professionalità, tale da instaurare un clima proficuo di trasparenza e collaborazione".
L'invito a riflettere senza reticenze sulla portata, sulla natura e sulle ripercussioni di un problema - quello del residuo solvente - che investe l'intero comparto della trasformazione, è stato a dire il vero accolto dagli utilizzatori nel verso giusto. E lo spirito positivo che ha animato gli interventi della tavola rotonda è stato di per sé motivo di soddisfazione generale. Anche perché, da più parti, è stata sottolineata la grande professionalità degli operatori italiani nel campo della trasformazione, ai quali viene ampiamente riconosciuta disponibilità ed elevata competenza tecnologica.
Bisogno di chiarezza
"Saper riflettere sulla realtà è prova di maturità culturale e segno di consapevolezza del proprio valore", e lo studio realizzato da Valter Rocchelli e dallo staff PDC, per conto di Giflex, dimostra che il settore del converting in Italia è vivo, propositivo, capace di darsi regole e basi di conoscenza importanti, da condividere con gli utilizzatori, così da gettare le basi per un miglioramento costante.
E che si tratta di fatti e non di parole lo ha ben puntualizzato il coordinatore del comitato tecnico Giflex, Pietro Lironi, che ha riassunto gli obiettivi dello studio sulla valutazione del residuo solvente.
Lo studio ha segnato per certi versi una tappa miliare nel mondo del converting italiano, per il tenore delle informazioni contenute e per la determinazione con cui Giflex ha deciso di renderle comuni ai suoi associati. Frutto di un lavoro durato tre anni, è stato scandito da una prima fase "in laboratorio" e da una seconda fase sperimentale (con la preparazione di campioni da parte di un qualificato converter associato a Giflex, che ha utilizzato un impianto pilota, su cui sono stati poi fatti test di ritenzione su modelli prestabiliti per tipologia di materiale e livelli di residuo solvente).
La pubblicazione dei risultati della ricerca sul residuo solvente nella stampa di imballaggi flessibile (curata dalla nostra rivista, Ndr) ha inteso dunque fornire una base comune di dati tecnico/scientifici al mondo della trasformazione italiana, composto da realtà industriali difformi (soprattutto in relazione alle strutture e alle possibilità di ricerca). Un mondo, che per tradizione, è da sempre orientato a sperimentare in proprio soluzioni e alternative, affidandosi all'esperienza, alle competenze personali e aziendali.
La base comune di informazioni costituisce, oggi, un supporto serio e incontrovertibile, proprio in quanto suffragato da dati di laboratorio e sperimentali, per la stesura dei capitolati di fornitura, sullesempio di quanto già fatto dal Giflex stesso.
Questioni di metodo
La sintesi precisa e puntuale fatta da Valter Rocchelli, che ha ricordato i momenti salienti della ricerca svolta in ambito PDC sul residuo solvente, ha consentito ai presenti di esprimere valutazioni proprio sulle metodologia adottata.
Va ricordato, anche in questa sede, che lo scopo dello studio è stato quello di dare una valenza oggettiva - in quanto numerica - al potenziale inquinante dell'acetato di etile e di individuarne i relativi limiti di rischio. In altre parole si sono volute individuare le ritenzioni reali per lacetato di etile, che possono dar luogo a rischio di danno organolettico.
Per queste ragioni, la ricerca è stata condotta in due fasi sperimentali distinte:
la PRIMA FASE "in vitro" (per valutare le soglie di percezione sensoriale di solventi utilizzati per la stampa rotocalco di materiali flessibili destinati al contatto con alimenti);
la SECONDA FASE "in vivo" (con la valutazione della ritenzione, del rilascio e del conseguente impatto olfattivo dellacetato di etile in materiali flessibili di diversa composizione stampati in rotocalco). Questa seconda fase ha consentito di verificare la risposta del modello matematico elaborato nella prima parte, relativamente ad alcuni dei materiali più spesso utilizzati.
Da sottolineare che, in generale, tutti i presenti hanno espresso grande apprezzamento per il lavoro di ricerca svolto, per la completezza delle analisi e la chiarezza dei risultati. Anzi, lo studio è stato giudicato in assoluto, uno dei lavori più significativi e allo stato dell'arte sulle problematiche della ritenzione solvente. Fermo restando il giudizio positivo sulle metodologie seguite, sia nella fase "in vitro" sia in quella "in vivo", sono emerse posizioni articolate in merito alla correlazione tra test strumentali e sensoriali, in genere ampiamente utilizzati dagli end user.
La scelta italiana
Sul fronte industriale, i risultati dello studio hanno testimoniato che la scelta tecnologica operata dai converter italiani, con l'adozione del monosolvente nella stampa di imballaggio flessibile, è stata corretta, e non solo dal punto di vista ambientale (grazie al recupero del solvente, infatti, il bilancio ambientale è favorevole).
Sia nella fase di laboratorio sia in quella sperimentale, lo studio ha infatti rivelato che la scelta dell'acetato di etile è stata felice, grazie alle caratteristiche intrinseche di questo solvente rispetto ad altri.
Da mettere in evidenza, a questo proposito, "l'imprimatur" della dottoressa Maria Rosaria Milana, dell'Istituto Superiore di Sanità, che ha parlato - in occasione della presentazione dello studio avvenuta a marzo 2003 durante lultima edizione di Ipack-Ima - della non pericolosità dell'acetato di etile dal punto di vista tossicologico, unico solvente realmente misurabile nella maggior parte dei casi in stampati in roto con l'impiego di monosolvente.
In questo contesto, il richiamo del Giflex agli end user è apparso chiaro: nella valutazione del monosolvente deve rientrare anche la consapevolezza che, in una miscela di solventi, si possano subdolamente "celare" taluni componenti con un impatto molto negativo sul prodotto.
Daltronde, anche lindustria alimentare, almeno in alcuni casi, sta lavorando sui microinquinanti, ovvero sugli ausiliari di produzione, adottando una logica del tipo lista positiva.
Partendo infatti dallevidenza che lacetato di etile spesso non è il principale responsabile dellodore dei materiali, si è scoperto, sulla base delle esperienze accumulate nel tempo, che è necessario evitare "sinergie negative" di questo solvente con una serie di sostanze utilizzate, anche a insaputa del trasformatore, per conferire, ad esempio, qualità particolari a inchiostri, vernici e adesivi, oppure presenti, come impurità, nel solvente stesso. Da ciò deriva che la collaborazione tra produttori di materie prime, di film e trasformatori è indispensabile per fare progressi nello studio della contaminazione organolettica in generale.
Delle materie prime
Lobiettivo prioritario dellindustria alimentare è certamente quello di evitare il rischio di danni organolettici ai prodotti. Detto questo non bisogna scadere in grossolane semplificazioni facendo confusione tra odore e residuo solvente.
Le materie prime nel loro insieme (film, adesivi, inchiostri) hanno odori e sapori "propri" e anche i materiali accoppiati non stampati o neutri - come ha dimostrato la ricerca - possono avere un proprio valore di ritenzione solvente.
Al riguardo Giflex sta portando avanti una revisione dei capitolati di acquisto (di cui si prevede la pubblicazione entro la prima metà del 2004) avente per oggetto proprio lodore intrinseco delle materie prime. Lobiettivo è di permettere al trasformatore di sapere in partenza quello a cui può andare in contro (acquistando una certa materia prima); ma anche il produttore di materia prima deve sapere a quali problemi ovviare, per offrire un prodotto adeguato alle esigenze dell'utilizzatore.
Alla scopo si intende creare una "commissione mista" fra utilizzatori e produttori di imballaggi, in grado di interloquire con i produttori di materie prime, il che rappresenterebbe un momento importante nel lavoro comune di miglioramento.
Condividere cultura
e vantaggi
Questo obiettivo è stato largamente condiviso dai rappresentanti dellindustria alimentare, che si sono dichiarati disponibili a collaborare anche con i fornitori di materie prime con lobiettivo di superare la logica della "contaminazione del prodotto alimentare". Lorientamento è di adottare un approccio che preveda l'assenza di odori estranei nel complesso dei materiali da imballaggio, stampati o neutri, che vengono utilizzati.
La minimizzazione dei fattori di rischio, e conseguentemente anche del livello di residuo solvente nei materiali da imballaggio, può apparire una provocazione, ma segna di fatto la direzione del percorso da seguire. In questottica i converter chiedono di generalizzare una prassi, per altro già fatta propria da molti gruppi industriali, che consiste nello stabilire non solo un valore di accettabilità globale ma anche per singolo solvente, in funzione dello specifico potere inquinante, dal punto di vista dellodore e della tossicità.
A questo scopo, Giflex sta portando avanti un lavoro di revisione dei capitolati di fornitura - pubblicati nel 2002 - così da fissare, in collaborazione con gli utilizzatori, valori distinti di ritenzione solvente massimo ammissibile, in base alla composizione dei materiali e alla coprenza di stampa. Questi due principi hanno caratterizzato anche il lavoro di ricerca svolto da PDC e i risultati hanno confermato che ci sono differenze nel comportamento delle diverse strutture (monofilm, accoppiati duplex e triplex, con o senza barriera), nonché rispetto alla coprenza di stampa.
Lo studio ha infatti ribadito che, alcuni "sistemi materiali" possono offrire una barriera adeguata, tale da soddisfare le necessità applicative, senza esasperare le richieste in fatto di residuo solvente. Durante il dibattito molti degli interventi hanno, in effetti, sottolineato che potrebbe quanto mai essere opportuno distinguere i valori di residuo solvente in base al tipo di materiale, senza fissare un valore unico ammissibile, ovvero arrivare a considerare il residuo solvente come uno dei parametri della specifica tecnica del materiale, e non del capitolato generale di fornitura.
La variabile Capitolati
Per dovere di cronaca va sottolineato che alcuni utilizzatori continuano a considerare l'analisi del residuo solvente come come uno "screening successivo" alla segnalazione di odorosità rilevata tramite analisi sensoriali.
Nella pratica, quando il test sensoriale fornisce risultati dubbi o di "non accettazione", prima di rifiutare un materiale si passa a un'analisi strumentale indirizzata a determinare l'entità del residuo solvente, oppure di altri possibili contaminanti.
Lindustria alimentare tende a tutelarsi imponendo specifiche limitazioni per quanto riguarda il residuo solvente totale complessivo, con valori, in alcuni casi, decisamente restrittivi in merito all'acetato di etile.
Ma, ricollegandoci al lavoro di Rocchelli e del Giflex, va notato che la valutazione del risultato dei test organolettici dipende molto dal tipo di alimento confezionato. A questo punto, siccome uno dei temi di discussione riguarda i limiti stabiliti nei capitolati, non sembra corretto parlare di un limite generale, e neanche di un limite di capitolato specifico per tipo di industria, ma bisognerebbe procedere per capitolati differenziati per prodotto, se non per tipologia di confezionamento, nonché per rapporto tra superficie del packaging e quantità di prodotto confezionato.
Per complicare ulteriormente la situazione andrebbe poi presa in considerazione unulteriore variabile, quella relativa alle modalità di conservazione del prodotto durante il ciclo logistico, distributivo e del consumo .
Progettare
gli acquisti
Il problema del residuo solvente è quindi da mettere in diretta relazione con i cambiamenti che stanno interessando le procedure e le modalità di acquisto dei materiali da imballaggio. Le aste on line ne sono un esempio eclatante: in queste sedi, spesso si devono definire dei prezzi di fornitura affidandosi a descrizioni sintetiche e a capitolati che esprimono un "valore" unico di residuo solvente per i materiali più diversi (alluminio laccato o stampato, monofilm, accoppiati con elevate coprenze, ecc.).
I produttori di imballaggi flessibili sono preoccupati di questa eccessiva semplificazione, che può condizionare la possibilità di realizzare un prodotto idoneo al prezzo migliore. Un obiettivo che invece può essere ottenuto, ragionando di volta in volta sul tipo di imballaggio da impiegare, in funzione della sua applicazione e ai fattori di rischio che è necessario garantire.
Daltronde, il coinvolgimento del converter anche in fase di definizione delle caratteristiche dell'imballaggio, è un aspetto troppo spesso trascurato e senza dubbio da rivalutare.
Anche in fatto di solventi, una scelta opportuna della struttura dei materiali può evitare di esasperare certe scelte tecnologiche, lasciando spazio alla sperimentazione di nuove soluzioni in grado di soddisfare, non solo i requisiti di protezione delle caratteristiche organolettiche del prodotto, ma anche gli aspetti legati ai costi (per buona pace degli uffici acquisti) e quelli di migliore macchinabilità, a fronte di velocità di confezionamento sempre più elevate.
L'imballaggio è un oggetto decisamente complesso ed è solo ottimizzando lefficienza dell'intera catena produttiva che si ottengono economie reali. Altrimenti significa scaricare i propri costi sul soggetto più "debole" (ovvero, in questo caso, i trasformatori).
Incidenti di percorso:
il fattore tempo
La pratica insegna che, spesso, i reclami a seguito di test sensoriali non sono nella maggior parte dei casi da imputare a un elevato valore di residuo solvente - soprattutto se si tratta di acetato di etile - ma sono riconducibili a contaminazioni accidentali dellimballaggio, derivanti dai mezzi e dalle modalità di trasporto e stoccaggio.
Ciò non toglie che nella fornitura dei materiali possano capitare spiacevoli incidenti di percorso. Si tratta di eventi accidentali, soprattutto perché i trasformatori negli ultimi anni hanno fatto notevoli investimenti in tecnologia e in impiantistica (questo per assicurare la migliori garanzie), e tutte le aziende più grandi sono certificate allo scopo di offrire un prodotto il più aderente possibile ai capitolati.
Gli investimenti hanno riguardato impianti e macchine da stampa, ma anche i sistemi di rilevazione della concentrazione del livello di ritenzione di solventi, che ora sono praticamente "in linea" o per lo meno situati molto vicini alle macchine da stampa, per permettere di offrire garanzie migliori che in passato.
Ma il contenzioso tra converter ed end-user è spesso alimentato anche da incomprensioni circa i tempi di consegna dei materiali.
Si tratta di un tema che non ha un'incidenza così aristocratica e tecnologica come quella descritta nello studio del Giflex, ma che comunque risulta fondamentale per i trasformatori, relativamente alla cessione di odori, in termini generali. Andare in rottura di stock e dover provvedere ad un approvvigionamento di emergenza può esporre al rischio di forniture di materiali fuori standard, e questo non è positivo per nessuno.
Il futuro è nel dialogo
Per tirare le fila del dibattito, parrebbe che il problema del residuo solvente sia importante, ma quasi mai determinante, in relazione alla tematica più generale della "cessione di odori" da parte dell'imballaggio all'alimento. Fermo restando che l'obiettivo dellindustria alimentare è di dare al consumatore un prodotto garantito e sicuro (dal punto di vista igienico e organolettico), l'imballaggio deve essere in grado di assolvere correttamente alla sua funzione. Allo scopo sono necessarie un'attenta progettazione, ma soprattutto un rapporto più stretto tra utilizzatori/converter/produttori di materiali e ben strutturate e coerenti occasioni di incontro e confronto.
Giflex ha rotto il ghiaccio e si attiverà quanto prima per testimoniare nei fatti che il mondo del converting italiano è composto da aziende di altissima levatura: la professionalità che contraddistingue il comparto, la volontà dei singoli che sanno spendere le proprie conoscenze in mirati lavori di approfondimento, stanno infatti a dimostrare la bontà e l'eccellenza della trasformazione italiana.
|
|
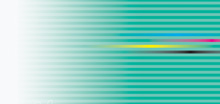
Flexible films, solvent residue and the worth of a segment
Ce nest quun début
Account of the round table promoted by Giflex: converters and end users from the food sector met up to discuss solvent residue in flexible packaging. From the evaluation of the methodology for rating acceptable perception thresholds for ethyl acetate and its real incidence on foodstuffs organoleptic properties, those present soon went on to consider the many other variables at play, among which the more general problem of packaging odour. Thus contributing to common knowledge (and a common asset).
Luciana Guidotti, Stefano Lavorini
On the basis of the results that emerged during the study made by PDC, and culminating in the publication of the Technical study Rotogravure printing of flexible film and the problem of residue solvents(*), Giflex (the work group that comes under Assografici and that represents around 80% of Italian converting activity) is proceeding in its revision of the technical specifications that are an integral part of supply contracts. In the meantime it is promoting occasions for debate, currently involving the large Italian and foreign flexible packaging users, but also prospecting further undertakings extended to raw materials producers and operators in distribution.
On its side of things, Giflex can field tried and proven knowledge of the thorniest problems that mark the activity of Italian converting, while inviting suppliers and customers to express themselves freely in a debate that can only be advantageous for all.
This choice of approach was also reiterated in occasion of the encounter held at October at Villa Torretta, close to Milan, and featured in Giflex President Ruggero Gerosas appeal to the participants so that they «create an open exchange between professional standings, in order to establish a fruitful climate of transparency and cooperation».
The invitation to openly reflect on the scope, on the nature and the repercussions of a problem - that of solvent residue - that affects their entire converting segment, was taken in the right spirit by users. And indeed the positive atmosphere in which the round table talks were held was in itself a reason for satisfaction all round. This also thanks to the general recognition of great professionality attributed to Italian operators in the converting field, of their preparedness and their advanced technological skills.
Need for clarity
«Being able to reflect on reality is proof of ones cultural maturity and sign that you know your own worth», and the study made by Valter Rocchelli and by the PDC staff for Giflex shows that the converting sector in Italy is alive, full of proposals, capable of laying down rules and a basis of common knowledge to be shared with the users, this so as to lay the basis for ongoing common improvement.
And that we are talking about deeds and not words was made clear by the Giflex technical committee coordinator Pietro Lironi, who summed up the objectives of the study on rating residual solvents.
The study has to a certain extent marked out a milestone in the world of Italian converting, due to the quality of the information contained and due to Giflexs determination to share its findings with its associates. The result of work that has gone on for three years, constituted by an initial laboratory phase and by a subsequent experimental phase (where the samples were prepared by a qualified Giflex associated converter using a pilot plant, where retention tests were carried out on models of a set material type and solvent residue level).
The publication of the results of the study on solvent residue in printing on flexible packaging (edited by our magazine, E.n.) to hence give a common basis of technical/scientific data for the Italian world of converting, constituted by a variety of types of industrial concerns (different aboveall in terms of structure and the extent of their research facilities). A world that by tradition has always been inclined to experiment its own solutions and alternatives, relying on experience, on personal and company skills.
The common basis of information today constitutes a serious and indisputable platform for making out supply contracts, due to the very fact it is confirmed by laboratory and experimental work, this on the basis of the work already carried out by Giflex itself.
Questions of method
The precise and detailed synthesis made by Vater Rocchelli, who cited the key stages of the PDC study on solvent residue, enabled those present to give their own rating of the methodology adopted. It should here too be remembered that the purpose of the study was that of objectively rating the pollutant potential of ethyl acetate and in terms of figures, also rating the relative risk limits. In other words it was question of identifying the actual retention rates for ethyl acetate, that might lead to risks of organoleptic damage. This is why the study was carried out in two distinct experimental stages:
the First Phase in vitro(to rate the sensorial perception thresholds for solvents used for rotogravure printing of flexible materials for contact with foodstuffs);
the Second Phase in vivo (with rating of retention, release and consequent olfactive impact of ethyl acetate on rotogravure printed flexible materials of various composition). This second phase has enabled the verification of the response of the mathematical model devised in the first section, this concerning some of the most-used materials.
It should be underlined that in general all those present expressed great appreciation for the research work carried out, for the completeness of the analysis and the clarity of the results. Indeed the study was judged of the highest importance and at the state-of-the-art of the problems of solvent retention. While the positive judgments on the methodology followed still hold, both in the in vitro and the in vivo phases, different positions emerged in terms of the correlation between instrument and sensorial tests, in general broadly adopted by the end users.
The Italian choice
On the industrial front, the results of the study have testified that the technological choice made by the Italian converters to adopt monosolvents in printing flexible packaging was correct, and this not only from an environmental point of view (the resulting solvent recovery has in fact led to a favorable environmental balance).
The laboratory tests and the experimental phase carried out as part of the study have in fact revealed that the choice of ethyl acetate was a good one, thanks to the intrinsic characteristics of this solvent compared to others.
To be highlighted on this point the imprimatur of Dr. Maria Rosaria Milana, of the Istituto Superiore di Sanità, who spoke - on occasion of the presentation of the study made March 2003 during the last edition of Ipack-Ima - of ethyl acetates non dangerousness from the toxicological point of view, it being the only solvent that is actually mainly measurable in rotogravure printing using a monosolvent.
Here Giflexs call to the end user appears clear: in rating the monosolvent you also have to consider that a solvent mixture may surreptitiously contain components that have a highly negative impact on the product.
Indeed in at least a number of cases the food industry is also working on micropollution, or that is on production auxiliaries, adopting a positive list type logic.
In fact starting off from the proof that ethyl acetate is often not the main cause of material odour, it was discovered, on the basis of experience built up in time, that the negative synergies of this solvent with a series of substances used should be avoided. These are substances of which the converter is often unaware of, used for example for giving inks, lacquers and adhesives special qualities, or present as impurities in the selfsame solvent. This indicates that cooperation between raw material producers, film producers and converters is indispensable in order to attain progress in the study of organoleptic contamination in general.
Raw materials
The priority objective of the food industry is certainly that of avoiding the risk of organoleptic damage to the product. Having said this one should not fall into gross simplifications by confusing odour with solvent residue.
Raw materials all told (films, adhesives, inks) have their own odours and tastes and even non printed or neutral laminated materials - as the study has shown - can have their own solvent retention rate.
On this count Giflex is bringing about a revision of the purchasing contract (the publication of which is scheduled for the first half of 2004) the object being the intrinsic odour of raw materials. The objective is to allow the converter to know right from the start what he might be in for (buying a given material); but the raw material producers also has to know the problems he has to tackle, to offer a product suited to the users needs.
To this purpose a mixed commission of packaging users and producers, capable of dialoguing with raw material producers, is to be set up, that should stand as a key instance in the common striving towards improvement.
Share culture
and advantages
This objective is broadly shared among food industry representatives, that declared themselves to be also ready to cooperate with raw material suppliers in order to overcome the contamination of food product logic. The tendency is to adopt an approach leading to an absence of extraneous odours in all packaging materials that are used, be these printed or neutral.
Minimizing the risk factor, and hence also the level of residue solvents in packaging materials, may appear provocative, but it in fact marks the direction to be taken.
In this line of things the converters ask that a practise, already adopted by many industrial groups, be generalised. This consists in not only establishing an overall acceptability rating but also establishing an acceptability rating for the single solvent, this in terms of its specific polluting power, and in terms of odour and toxicity.
To this purpose, Giflex is carrying out a revision of supply contracts - published in 2002 - in cooperation with the users in order to set max admissible solvent retention rates on the basis of material composition and print coverage. These two principles have also featured in the studies carried out by PDC, and the results have in fact confirmed that the various structures (monofilm, duplex and triplex laminates, with or without barrier) perform differently, and also offer differences in print coverage.
The study has in fact underlined that some material systems can offer an adequate barrier, enough to satisfy the applicative needs, without exceeding the mark in terms of residual solvents. During the debate many of those who intervened in actual fact stated that it might now more than ever be good idea to distinguish the residual solvent rates on the basis of material types, without setting a sole admissible rating, or that is come to consider the solvent residue as one of the parameters of material technical specifications, and not of the general supply contracts.
The contract variable
Just for the record it should be underlined that some users continue to consider the analysis of solvent residue as a subsequent screening following on from smell registered through sensorial analysis.
In other words, if the material stinks first and foremost it is not put into production and only afterwards is a check in order to discover the source of pollution carried out.
In practise, when the sensorial test leads to dubious results or non acceptance, before refusing a material one goes on to an instrumental analysis carried out to rate the entity of residual solvent, or other possible contaminants.
The food industry tends to protect itself imposing specific limits as far as the total overall residual solvent is concerned, with rates that are in some cases decidedly restrictive concerning ethyl acetate. But going back to the work of Rocchelli and that of Giflex, it should be noted that the evaluation of the result of organoleptic tests depends a lot on the type of food packed.
On this point, in that one of the discussion themes regards the limits set in the contracts, it does not seem correct to speak of a general limit, and neither of a specific contract limit per type of industry or concern, but one should differentiate the contracts according to the product, if not also by type of pack, as well as also by ratio between the surface of the pack and the quantity of product packed.
To further complicate the situation one has to consider a further variable, that of the mode of preservation of the product during the logistics, distribution and consumption cycle.
Planning
your purchases
The problem of residue solvent is placed in direct relation with the changes that are affecting the procedure and the mode of purchase of packaging material. The on line auctions are a blatant example: here, one has to often define supply prices based on summary descriptions and contracts that express a sole rating of solvent residue for materials that are very different (coated or stamped aluminium, monofilms, laminates with high printing coverage, etc.).
Flexible packaging producers are worried about this excessive simplification, that can condition the possibility of creating an acceptable product at the best price. An objective that can though be obtained, reasoning as the case has it on the type of packaging to be used, in function of its application and the risk factors that need to be guaranteed.
And in fact, also involving the converter in the phase of definition of the packaging characteristics, is an aspect that is all to often neglected and without a doubt needs to be reconsidered.
Also in terms of solvents, the right choice of the material structure can avoid exasperating given technological choices, leaving space to experiment new solutions capable of not only satisfying the requisites of protecting the organoleptic features of the product, but also aspects connected to costs (and keep the purchasing office happy) and those of the best machineability, this in the face of ever higher packaging speeds. Packaging is a decidedly complex object and it is only by optimizing the efficiency of the entire production chain that real savings are obtained. Otherwise it means offloading ones costs on the weakest subject (or that is in this case the converter).
Mishaps and upsets:
the time factor
Practise teaches one that often complaints following on from sensorial tests are not in the most cases to be put down to a high rate of solvent residue - aboveall if it is a question of ethyl acetate - but can be attributed to accidental contamination of the packaging, deriving from means and modes of transport and storage. This does not cancel out the fact that in the supply of materials unfortunate mishaps can occur: these are accidental events, aboveall because the converters in these last years have made considerable investments in technology and systems (this to ensure greater guarantees), and all the larger concerns are certified for the purpose of offering a product that is as close as possible to what is listed in the contracts.
The investments have involved print machines and systems, but also systems for revealing the concentration of the level of retention of solvents, that by now are practically in line or at least situated very close to the printing machines, to give greater guarantees than in the But the dispute between the converter and end user often arises from misunderstandings as to the delivery times of the materials: it is a subject that does not have the overbearing and technological incidence described in Giflexs study, but that is all the same fundamental for the converters, this in general terms covering the ceding of odours.
Running out of stock and having to resort to an emergency procurement may mean risking the supply of non-standard materials, and this is detrimental to all sides.
The future lies in dialoguing
To draw things to a conclusion, it would appear that the problem of solvent residue is an important one, but that it is never decisive, in relation to the more general subject of ceding of odours by the food packaging. Considering that the objective of the food packaging industry is to give the consumer a guaranteed and safe product (from the hygienic and organoleptic point of view), the packaging has to be capable of correctly fulfilling its function. This is to be achieved by careful designing and planning, but aboveall by closer relations between the material user/converter/producer and well structured and ongoing occasions for encounters and exchanges. Giflex has broken the ice and is committed to bearing witness to the fact that the Italian world of converting is made up of high ranking concerns: the professionality that stands out in the segment, the will of single persons who are prepared to invest their knowhow in further research work, testifies the to the effectiveness and excellence of the work of Italian converters.
|